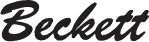
Instruction Manual – Model CF2300A Oil Burner
11
Form 6104 BCF-23-R0399
Sequence of operation — typical
NOTE: The following sequence is based on using a type B
fuel unit, with pump-mounted by-pass valve. The by-pass valve
operation is reversed for a type H fuel unit. That is, the by-
pass valve is powered at low fire instead of being powered at
high fire.
1. On call for heat from the appliance operating controls (and
the circuit from T to T of the R8184 closed), power is
applied to the R8184 black wire (BK).
2. The R8184 applies 120 volts to the orange wire (OR), acti-
vating the burner motor (M1) and the ignition transformer
(TR). The oil pump is operated by the burner motor, so oil
pressure is delivered to the oil valve inlets.
3. Power is applied to the oil valve circuit. If optional timer,
(TM), is installed, oil flow will be delayed for the timer
duration, thus providing a prepurge period. When the timer
times out, oil valves (S1 and S3) are activated, allowing
oil to flow to the nozzle.
4. With the low-fire hold switch (LFHS) in the “IN” position,
the burner will remain at low fire. With no power applied to
the by-pass valve (S2), oil by-passes internally in the fuel
unit, reducing the pressure sent to the oil nozzle.
5. When the low-fire hold switch is moved to the “OUT”
position, the damper motor (DM) will be activated. This
will begin opening the air damper.
Prepare the burner for start-up
Start-up checklist – Verify the following before attempting to start burner.
❏ Fuel supply line is correctly installed, the oil tank is
sufficiently filled, and shutoff valves are open.
❏ Burner is securely mounted in appliance, with pressure
firing plate and gasket installed for pressurized chamber
application.
❏ Appliance has been filled with water (boilers) and controls
have been operationally checked.
❏ Burner has been installed in accordance with appliance
manufacturer’s instructions (when available).
❏ Also refer to appliance manufacturer’s instructions (when
available) for start-up procedures.
❏ Combustion air supply and venting have been inspected
and verified to be free of obstructions and installed in
accordance with all applicable codes.
❏ Oil nozzle has been selected correctly and securely installed
in the nozzle adapter.
❏ Fuel unit by-pass plug and external by-pass loop — from
Return port to pump Inlet — have been installed for one-
pipe oil systems. By-pass plug is installed for two-pipe oil
systems.
❏ Fuel connection to nozzle line assembly is secure.
❏ Dimension Z has been set per this instruction manual.
6. When the damper motor end switch is tripped, oil valve
(S2) is activated, stopping by-pass flow inside the fuel
unit and providing full pressure (300 psig) at the oil nozzle.
The burner is now at high fire. The damper motor end switch
is set to operate before the damper has reached full open
to assure a smooth transition to high fire.
7. If a high/low-fire control is installed at H/L, this control
will cycle the firing rate automatically during an operat-
ing cycle.
8. At the start of the cycle, the R8184 begins checking for
flame signal between F and F. Flame must be established
within 15 seconds of initiation. If no flame is sensed after
15 seconds, the R8184 will terminate all power to the
blower and oil circuits, shutting the burner down. The con-
trol will electrically lock out.
• To reset the control after lockout, wait 2 to 3 minutes
after lockout to give the internal switch time to cool.
Then push the reset button on the primary control, al-
lowing the burner to operate in normal sequence.
• Troubleshoot the reason for flame sense failure.
9. When the call for heat signal terminates (at the black wire
of the R8184), the R8184 terminates power to all circuits,
closing the oil valves and stopping the burner motor.