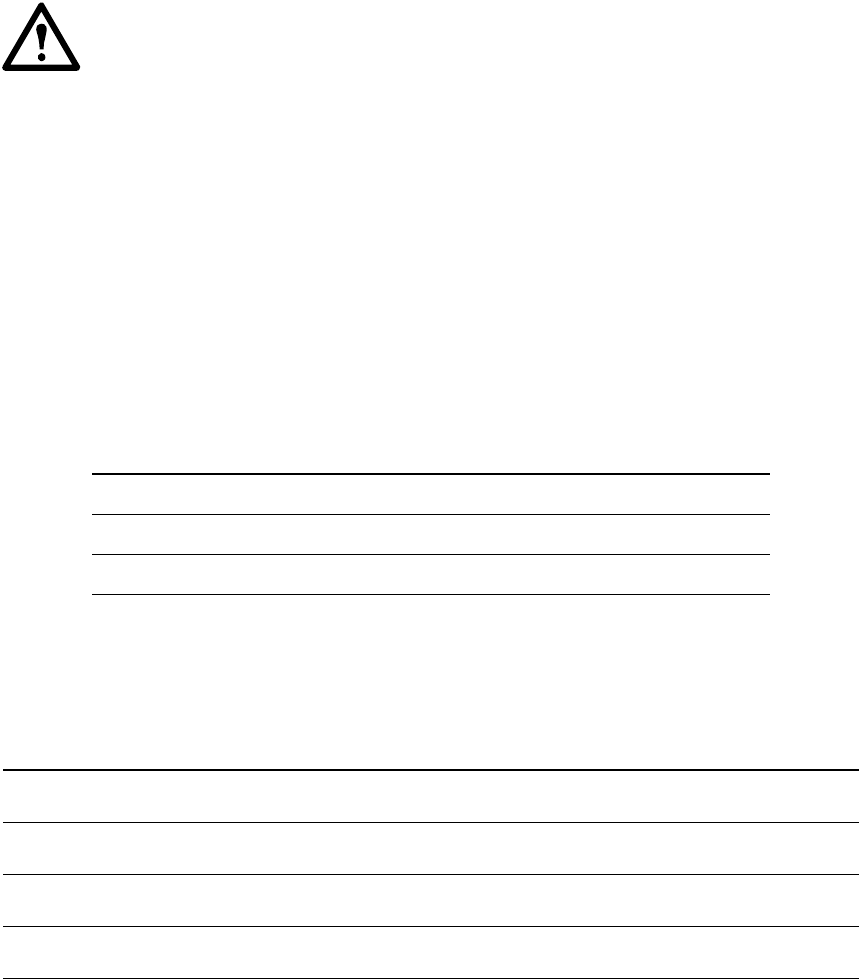
21InRow RD 10 kW Air Cooled Operation and Maintenance
Tune the PID loop
Tune the PID loop to optimize the performance of the cooling group.
Caution: This procedure must be performed by APC authorized personnel only. The PID
loop must be tuned after the equipment in the room is installed and running. The loop should
be tuned periodically to account for changes in the room load.
1. Adjust the integral and derivative constants to zero and the proportional constant to 1.0.
2. Set the temperature setpoint value and start the cooling group.
3. When the temperature reaches a stable value, increase the proportional constant by 0.5. If the
temperature does not respond to this change, adjust the setpoint.
4. Repeat step 3 until the temperature value starts to oscillate and the peak amplitude of the
oscillations is constant.
5. Note the time, in minutes, between the peaks of the oscillations. This is the Ultimate Period, P
U.
6. Note the value of the proportional constant. This is the Ultimate Gain, G
U.
7. Compute the PID constants using the table below. Use the equations for that control method in
the row to compute the values for each constant.
8. Set each constant according to these calculations.
You may need to further tune the PID loop in the following ways to account for changes in the room
load:
Control Method Proportional Integral Derivative
P 0.5*G
U
––
P + I 0.45*G
U
0.54*G
U
/P
U
–
P + I + D 0.6*G
U
1.2*G
U
/P
U
0.075*G
U
*P
U
Loop Behavior PID Tuning Correction
Slow response to temperature changes Increase the proportional multiplier or increase the
derivative multiplier.
Overcooling/undercooling after changes in the
room load or changes in setpoint
Increase the derivative or the proportional multiplier.
Environmental temperature never reaches the
setpoint
Increase the integral multiplier.
Overcooling/undercooling on constant room
load
Decrease the integral multiplier.