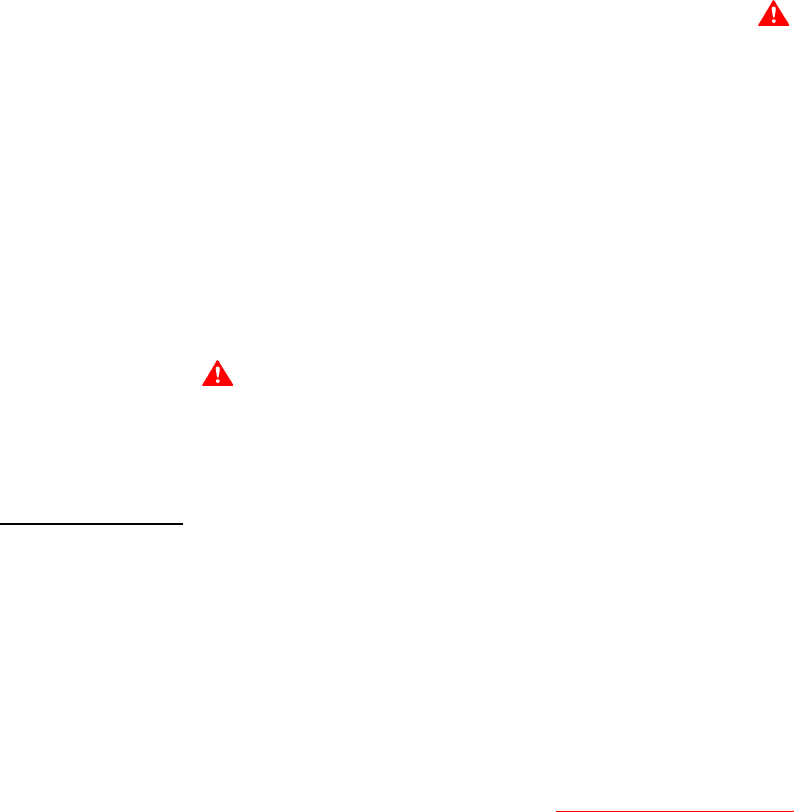
18
related to approximate water volume of the system. The system
should be turned on to circulate water mix for about one hour and
then flush clean with fresh water.
Before operating the boiler, the entire system must be filled with
water, purged of air and checked for leaks. Do not use Stop Leak or
other boiler compounds.
THE WATER HEATER SHOULD BE LOCATED IN AN AREA WHERE
THE GENERAL PUBLIC DOES NOT HAVE ACCESS TO BOILER
CONTROLS.
HOT WATER SUPPLY
BOILER INSTALLATION
WATER LINE CONNECTIONS
Where excessive heat exchanger condensation exists due to
continued low inlet water temperatures below 120°F (49°C), a
bypass balance loop must be installed. See Figures 10 and 12.
HARD WATER CONDITIONS
Where hard water conditions exist, water softening or the threshold
type of water treatment is recommended. This will protect the
dishwashers, coffee urns, water heaters, water piping and other
equipment. When water softening or water treatment is not practical,
a comparatively easy method of periodic lime removal from the unit
must be employed.
WARNING
LIME ACCUMULATION CAN REDUCE THE LIFE OF THE
EQUIPMENT, REDUCE EFFICIENCY AND WASTE FUEL. BOILER
FAILURE DUE TO LIME OR SCALE BUILDUP VOIDS THE
WARRANTY.
Tank Probe (Optional)
In addition to the Inlet and Outlet/ECO Probes, units can be
optionally equipped with a tank probe. The connection for the tank
probe is located in the 24VAC junction box at the rear of the unit.
The tank probe can be configured to control the staging of the unit.
See "Tank Probe Installation Procedure" section below for
additional information.
TANK PROBE INSTALLATION PROCEDURE
A tank probe is supplied with each hot water supply boiler (GW). To
connect the tank probe to the boiler, remove the cover from the
24VAC junction box at the rear of the unit. Connect the probe wires
across terminals 1 & 2. (The wires leading to the terminals will be
yellow.) Check the field connection diagram located on this cover of
the junction box to assure proper wiring.
Once the tank probe has been connected to the boiler, it must be
designated as the controlling probe for the system. This is
accomplished by changing two Dip Switch settings on the Central
Control Board. First, Dip Switch “SW1-4” must be set to the “ON”
position to designate the tank probe as the controlling probe.
Second, Dip Switch “SW1-1” must be set to the “OFF” position to
limit the maximum tank probe temperature for GW applications.
Failure to do this will void the warranty. If the tank probe is not
designated as the controlling probe, the staging of the unit will be
controlled by the inlet probe and will not use the desired tank
temperature as its base.
Refer to "Connection Diagram" in order to connect the tank probe
to the boiler. See Figures 12 and 15.
See section titled "Temperature Setpoints" for instructions on how
to set the temperature.
GAS CONNECTIONS
WARNING
THIS BOILER IS NOT INTENDED TO OPERATE AT GAS SUPPLY
PRESSURE OTHER THAN SHOWN ON THE RATING PLATE.
EXPOSURE TO HIGHER GAS SUPPLY PRESSURE MAY CAUSE
DAMAGE TO GAS VALVES WHICH CAN RESULT IN FIRE OR
EXPLOSION. IF OVERPRESSURE HAS OCCURRED SUCH AS
THROUGH IMPROPER TESTING OF GAS LINES OR EMERGENCY
MALFUNCTION OF THE SUPPLY SYSTEM, THE GAS VALVES MUST BE
CHECKED FOR SAFE OPERATION. MAKE SURE THAT THE OUTSIDE
VENTS ON THE SUPPLY REGULATORS AND THE SAFETY VENT VALVES
ARE PROTECTED AGAINST BLOCKAGE. THESE ARE PARTS OF
THE GAS SUPPLY SYSTEM, NOT THE BOILER. VENT BLOCKAGE
MAY OCCUR DURING ICE BUILD-UP OR SNOW STORMS.
WHEN LOCAL CODES REQUIRE A MAIN MANUAL SHUT-OFF
VALVE OUTSIDE THE BOILER JACKET, A SUITABLE MAIN
MANUAL SHUT-OFF VALVE MUST BE INSTALLED IN A LOCATION
COMPLYING WITH THOSE CODES.
IT IS IMPORTANT TO GUARD AGAINST GAS VALVE FOULING
FROM CONTAMINANTS IN THE GAS WAYS. SUCH FOULING
MAY CAUSE IMPROPER OPERATION, FIRE OR EXPLOSION. IF
COPPER SUPPLY LINES ARE USED THEY MUST BE
APPROVED FOR GAS SERVICE.
BEFORE ATTACHING THE GAS LINE BE SURE THAT ALL GAS
PIPE IS CLEAN ON THE INSIDE.
TO TRAP ANY DIRT OR FOREIGN MATERIAL IN THE GAS
SUPPLY LINE, A DIRT LEG (SOMETIMES CALLED DRIP LEG)
MUST BE INCORPORATED IN THE PIPING. THE DIRT LEG
MUST BE READILY ACCESSIBLE AND NOT SUBJECT TO
FREEZING CONDITIONS. INSTALL IN ACCORDANCE WITH
RECOMMENDATIONS OF SERVING GAS SUPPLIERS. REFER TO
NATIONAL FUEL GAS CODE, ANSI Z223.1 OR CAN/CSA -B149.1
(current edition).
THE BOILER AND ITS INDIVIDUAL SHUTOFF VALVE MUST BE
DISCONNECTED FROM THE GAS SUPPLY PIPING SYSTEM
DURING ANY PRESSURE TESTING OF THAT SYSTEM AT TEST
PRESSURES IN EXCESS OF 1/2 PSI (3.5 KPA).
THE BOILER MUST BE ISOLATED FROM THE GAS SUPPLY
PIPING SYSTEM BY CLOSING ITS INDIVIDUAL MANUAL
SHUTOFF VALVE DURING ANY PRESSURE TESTING OF THE
GAS SUPPLY PIPING SYSTEM AT TEST PRESSURES EQUAL TO
OR LESS THAN 1/2 PSI (3.5KPA).