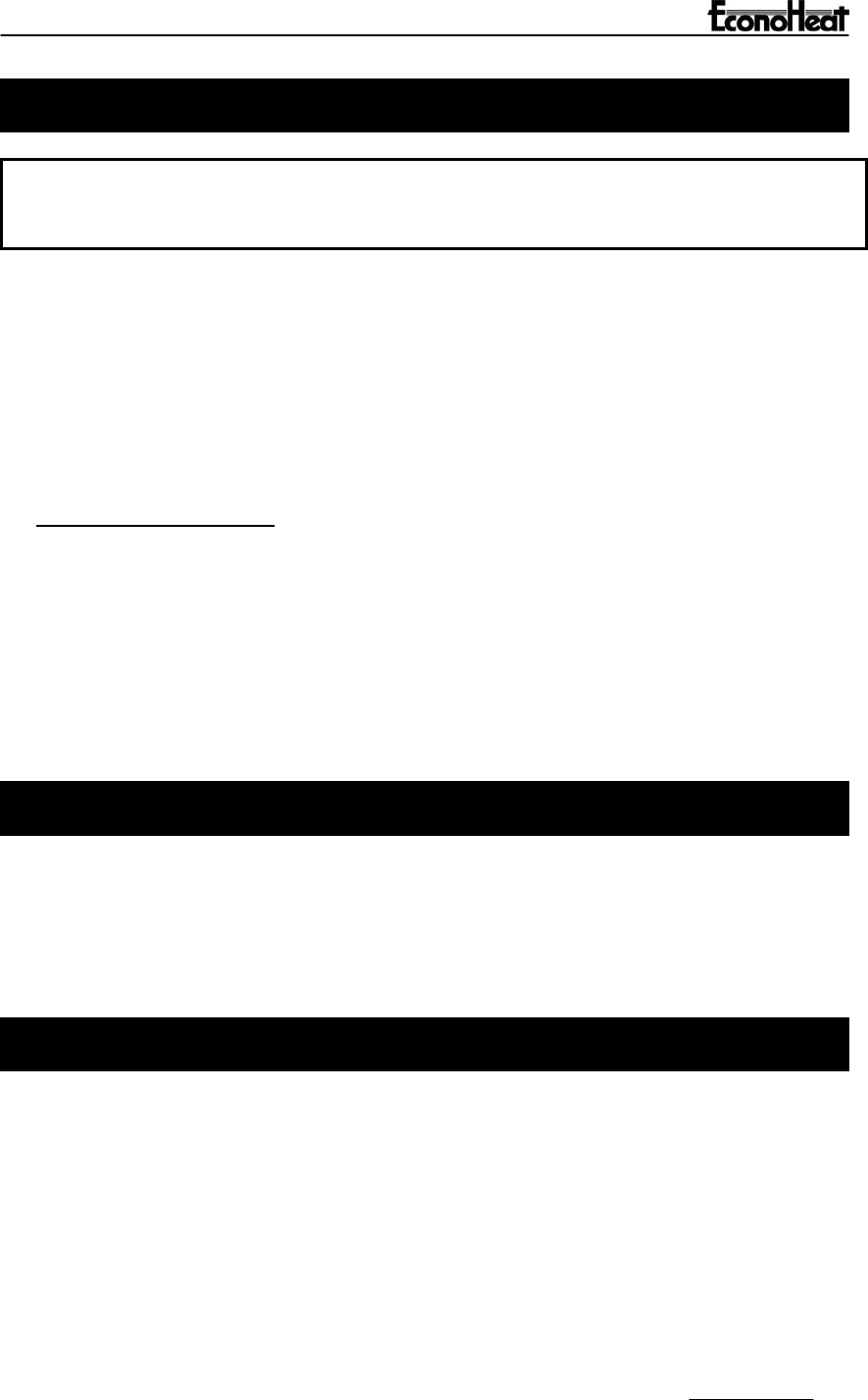
WARNING
DO NOT fire boiler without water or boiler sections will overheat and eventually crack
WASTE OIL BURNER STARTUP
6. IMPORTANT- Prior to starting the unit, pre-fill the filter and fuel line with oil to assist priming
procedure. Oil pump motor turns at low RPM’s and would take significant time to complete
priming process if not pre-filled. Make sure the oil supply line fittings are air tight. Vacuum
leaks are notoriously hard to find. Pressurizing the line with oil in it can help to locate leaks.
7. During the initial power up process the burner is locked out from energizing until the oil has
been properly pre-heated to operating thermo setpoint, approx 3 to 5 minute duration. Once
the oil has been pre-heated, power is then applied to burner componenets and oil pump.
8. Making sure the thermostat is turned off, apply power to the burner. Switch burner main
power switch to ON position. After allowing the oil pre-heater time to establish temperature
setpoint, approximately 5 minutes. Jump the “T” terminals on the Oil Primary (Figure 1).
Once the burner is running, temporarily jump the “F” terminals on the Oil Primary. This will
allow the burner to run during the pump priming process.
9. Priming the oil pump: Open bleeder valve one turn until all air is expelled (Figure 4). This
may need to be done twice to insure all air is removed. IMPORTANT: When fully purged and
flame is established remove temporarily jumpers on “F” terminals of the Oil Primary to allow
safety features of the unit to operate properly.
10. Adjust air supply of integrated air compressor to 8-12 P.S.I. This is factory preset, however,
due to freight handling settings may be compromised.
11. Combustion air band (Figure1) should be open approximately 1/2” or until flame is clear
yellow, not orange. Opening the air band too far may cause delayed in starting or even
prevent the flame from starting.
WATER TREATMENT
Generally no water treatment will be required. Care should be taken to ensure that the
system does not lose water from leaks, or continual relief valve operation since continual
make-up water will reduce boiler life.
FREEZE PROTECTION
Where freeze protection is required use antifreeze made especially for hydronic systems
such as inhibited Propylene Glycol. DO NOT use automotive type antifreeze. Follow
antifreeze manufacturer’s directions for quantity. A 50% solution provides protection to
–30 degree F. For boiler water content see page 11.
Installation, Operation, And Service Instructions 43