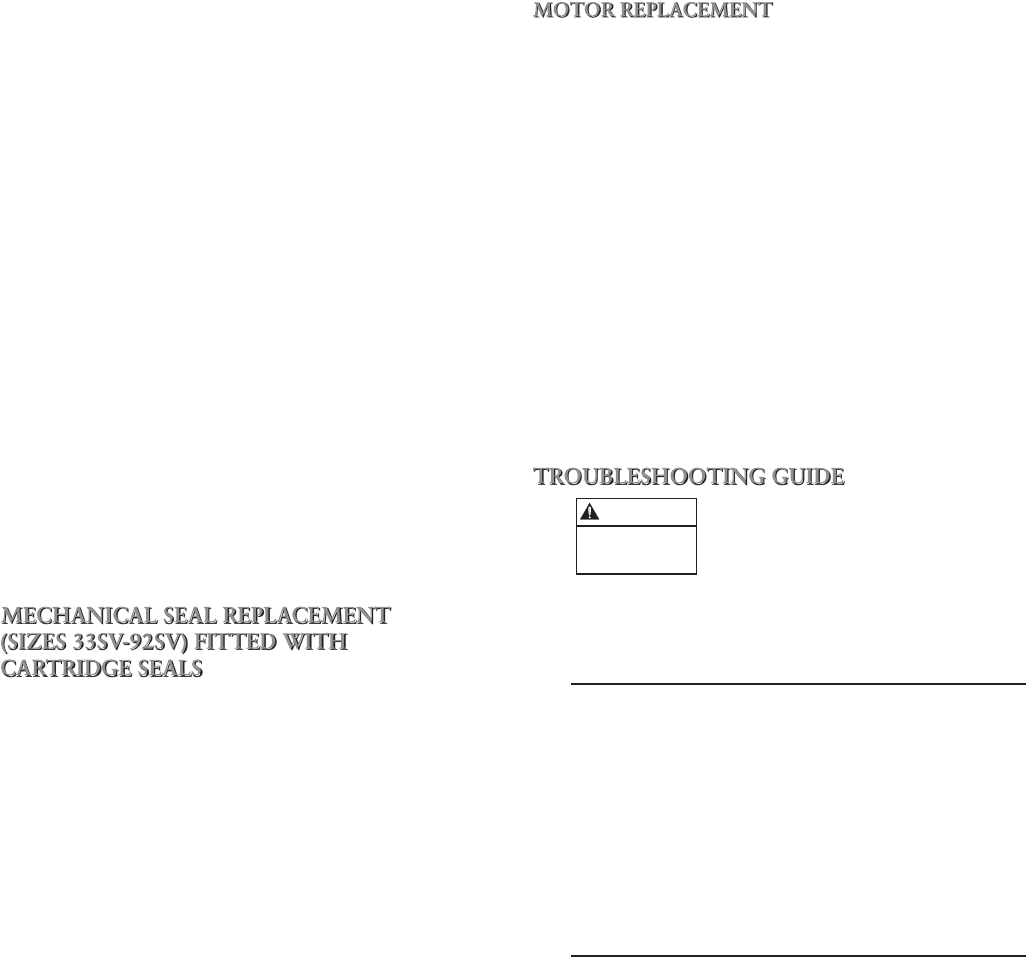
13
9. Install a new seal housing o-ring on the seal hous-
ing. A lubricant can be used to hold the o-ring on
the diameter of the seal housing.
Carefully reinstall the seal housing between the
pump and motor shaft and slide the seal housing
down the shaft into position. Use caution when
mounting the sealhousing between the
pump/motor shaft so that the seal face
on the stationary seat is not damaged.
See step 9 in Figure 5.
10. Reinstall the 4 hex cap screws, tightening
the screws evenly and then torquing them
to the values given in the engineering
data. See step 10 in Figure 5.
11. Reinstall the coupling pin and locate the
space shim on the shaft on the seal
housing. If the shim is not available, a
5 mm spacer can be used. See step 11 in
Figure 5.
12. Reinstall the coupling halves and evenly
tighten the coupling bolts and torque
them to the values given in the coupling
section. Remove the spacer shim and save
for future use. See step 12 in Figure 5.
13. Rotate the shaft by hand to insure that
the pump and motor rotate freely.
Reinstall the coupling guard.
14. The pump and system should be vented
prior to starting the pump. See Section 3,
page 8, for venting procedures.
1. Complete steps 1-4 as defined above for
conventional seals.
2. Loosen the 4 set screws located around the ID of
the pump shaft.
3. Remove the cartridge seal using the two tapped
holes provided on the gland of the cartridge seal
by threading two of the hex cap screws into these
holes and evenly tightening these screws. Lift and
remove the cartridge seal between the pump and
motor shaft.
4. Inspect the pump shaft for any burrs or debris.
Any burrs should be ground smooth with (fine
grit) emery paper.
5. Install a new o-ring on the turned fit of the new
cartridge seal. Lubricate the o-ring located in the
ID of the cartridge seal. Use a lubricant compat-
ible with the seal elastomers to hold the o-ring.
6. Install the new cartridge seal on the pump by care-
fully sliding it between the pump and motor shaft
and then sliding it into position.
7. Complete steps 11-14 as defined above for the
conventional seals.
8. After installing the coupling, tighten the four set
screws located in the collar of the cartridge seal to
secure the seal to the pump shaft.
9. Rotate the shaft by hand to insure that the pump
and motor rotate freely. Reinstall the coupling
guard.
10. Use vent connections on cartridge seal for proper
venting.
To remove the motor follow steps 1 through 4, as
provided in the “MECHANICAL SEAL REPLACE-
MENT” section of this manual.
For motor frames 213TC and larger, remove the 4
motor hex cap screws and the motor adapter.
Install the motor adapter flange onto the new motor,
torquing the 4 hex cap screws to the values provided
in the “ENGINEERING DATA” section of this
manual.
Complete the reassembly following steps 17 through
22 in the “MECHANICAL SEAL REPLACE-
MENT” section of this manual.
All additional unit service or maintenance, not ad-
dressed in this manual, should be performed at a
qualified service location. Contact your local dealer
or G&L Pumps distributor for assistance.
DISCONNECT AND LOCKOUT
ELECTRICAL POWER BEFORE
ATTEMPTING ANY MAINTE-
NANCE. FAILURE TO DO SO
CAN CAUSE SHOCK, BURNS
OR DEATH.
SYMPTOM
MOTOR NOT RUNNING
See Probable Cause – 1 through 5
LITTLE OR NO LIQUID DELIVERED BY PUMP
See Probable Cause – 6 through 12
POWER CONSUMPTION TOO HIGH
See Probable Cause – 3, 12, 13, 15
EXCESSIVE NOISE AND VIBRATION
See Probable Cause – 3, 6 - 8, 10, 12, 13, 16
PROBABLE CAUSE
1. Motor thermal protector tripped.
2. Open circuit breaker or blown fuse.
3. Impellers binding.
4. Motor improperly wired.
5. Defective motor.
6. Pump is not primed, air or gases in liquid.
7. Discharge, suction plugged or valve closed.
8. Incorrect rotation (three phase only).
9. Low voltage or phase loss.
10. Impellers worn or plugged.
WARNING
Hazardous
voltage