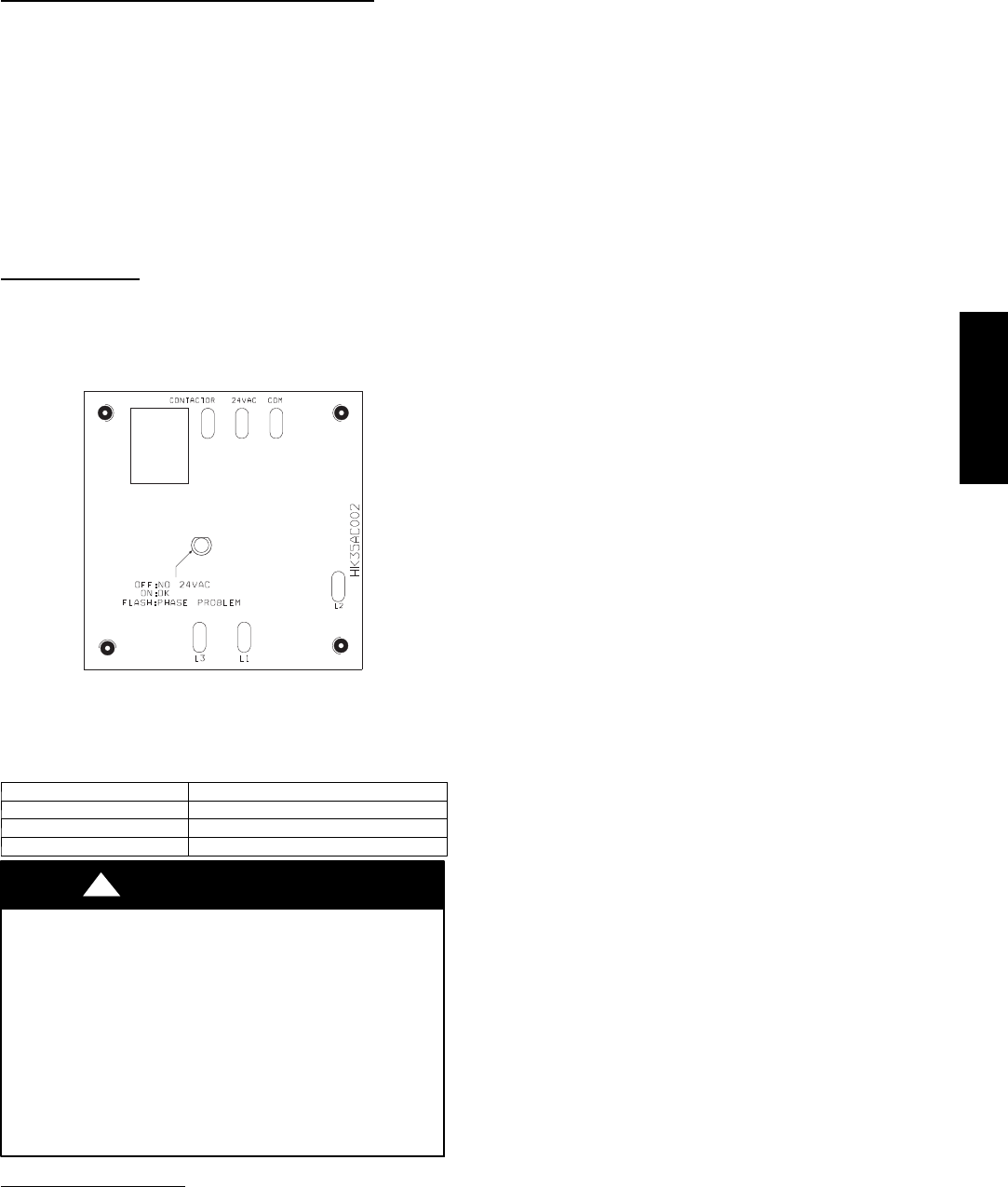
5
Follow these steps to properly start up system:
1. After system is evacuated, fully open liquid and vapor ser-
vice valves.
2. Unit is shipped with valve stem(s) front seated (closed) and
caps installed. Replace stem caps a fter system is opened to
refrigerant flow. Replace caps finger--tight and tighten with
wrench an additional 1/12 turn.
3. Close electrical disconnects to energize system.
4. Set room thermostat at desired temperature. Be sure set
point is below indoor ambient temperature.
5. Set room thermostat to COOL and fan control to ON or
AUTO mode, as desired. Operate unit for 15 minutes.
Check system refrigerant charge.
3--Phase Monitor
In 3--phase units a small circuit board is factory installed to monitor
line voltage. A small led will flash if a phase problem exists. See
code descriptions on monitor. If LED is flashing, disconnect
power to unit and interchange 2 field-- wiring leads on unit
contactor.
A00010
Fig. 6 -- 3--Phase Monitor Control
(Applies to 3--Phase Units Only)
Table 3 – Three--Phase Monitor LED Indicators
LED STATUS
OFF Nocallforcompressoroperation
FLASHING Reversed phase
ON Normal
UNIT DAMAGE HAZARD
Failure to follow this caution may result in equipment
damage or improper operation.
Ensure compressor rotation is c orrect.
S 3--phase scroll compressors are rotation s ensitive.
S A flash LED on phase monitor indicates reverse rotation.
(See Table 3)
This will not allow contractor to be energized.
S Disconnect power to unit and interchange 2 field-- wiring
leads on unit contactor.
CAUTION
!
Sequence of Operation
Turn on power to indoor and outdoor units. Transformer is
energized.
On a call for cooling, thermostat makes circuits R--Y and R--G.
Circuit R-- Y energizes contactor, starting outdoor fan motor and
compressor circuit. R--G energizes indoor unit blower relay,
starting indoor blower motor on high speed.
When thermostat is satisfied, its contacts open, de--energizing
contactor and blower relay. Compressor and motors stop.
If indoor unit is equipped with a time--delay relay circuit, the
indoor blower will run an additional 90 seconds to increase system
efficiency .
Check Charge
Factory charge amount and desired subcooling are shown on unit
rating plate. Charging method is shown on information plate inside
unit. To properly check or adjust charge, conditions must be
favorable for subcooling charging. Favorable conditions exist
when the outdoor temperature is between 70_F and 100_F
(21.11_C and 37.78_C), and the indoor temperature is between
70_F and 80_F (21.11_C and 26.67_C). Follow the procedure
below:
Unit is factory charged for 15ft (4.57 m) of lineset. Adjust charge
by adding or removing 0.6 oz/ft of 3/8 liquid line above or below
15ft (4.57 m) respectively.
For standard refrigerant line lengths (80 ft/24.38 m or less), allow
system to operate in cooling mode at least 15 minutes. If conditions
are favorable, check system charge by subcooling method. If any
adjustment is necessary, adjust charge slowly and allow system to
operate for 15 minutes to stabilize before declaring a properly
charged system.
If the indoor temperature is above 80_F (26.67_C), and the
outdoor temperature is in the favorable range, adjust system charge
by weight based on line length and allow the indoor temperature to
drop to 80_F (26.67_C) before attempting to check system char ge
by subcooling method as described above.
If the indoor temperature is below 70_F (21.11_C), or the outdoor
temperature is not in the favorable range, adjust charge for line set
length above or below 15ft (4.57 m) only. Charge level should then
be appropriate for the system to achieve rated capacity. The charge
level could then be checked at another time when the both indoor
and outdoor temperatures are in a more favorable range.
NOTE: If line length is beyond 80 ft (24.38 m) or greater than 20
ft (6.10 m) vertical separation, See Long Line Guideline for
special charging requirements.
Final Checks
IMPORTANT: Before leaving job, be sure to do the following:
1. Ensure that all wiring is routed away from tubing and sheet
metal edges to prevent rub--through or wire pinching.
2. Ensure that all wiring and tubing is secure in unit before
adding panels and covers. Securely fasten all panels and
covers.
3. Tighten service valve stem caps to 1/12-- turn past finger
tight.
4. Leave Owner’s Manual with owner. Explain system opera-
tion and periodic maintenance requirements outlined in
manual.
5. Fill out Dealer Installation Checklist and place in customer
file.
CARE AND MAINTENANCE
For continuing high performance and to minimize possible
equipment failure, periodic maintenance must be performed on this
equipment.
Frequency of maintenance may vary depending upon geographic
areas, such as coastal applications. See Owner’s Manual for
information.
113A / 114A / 116B