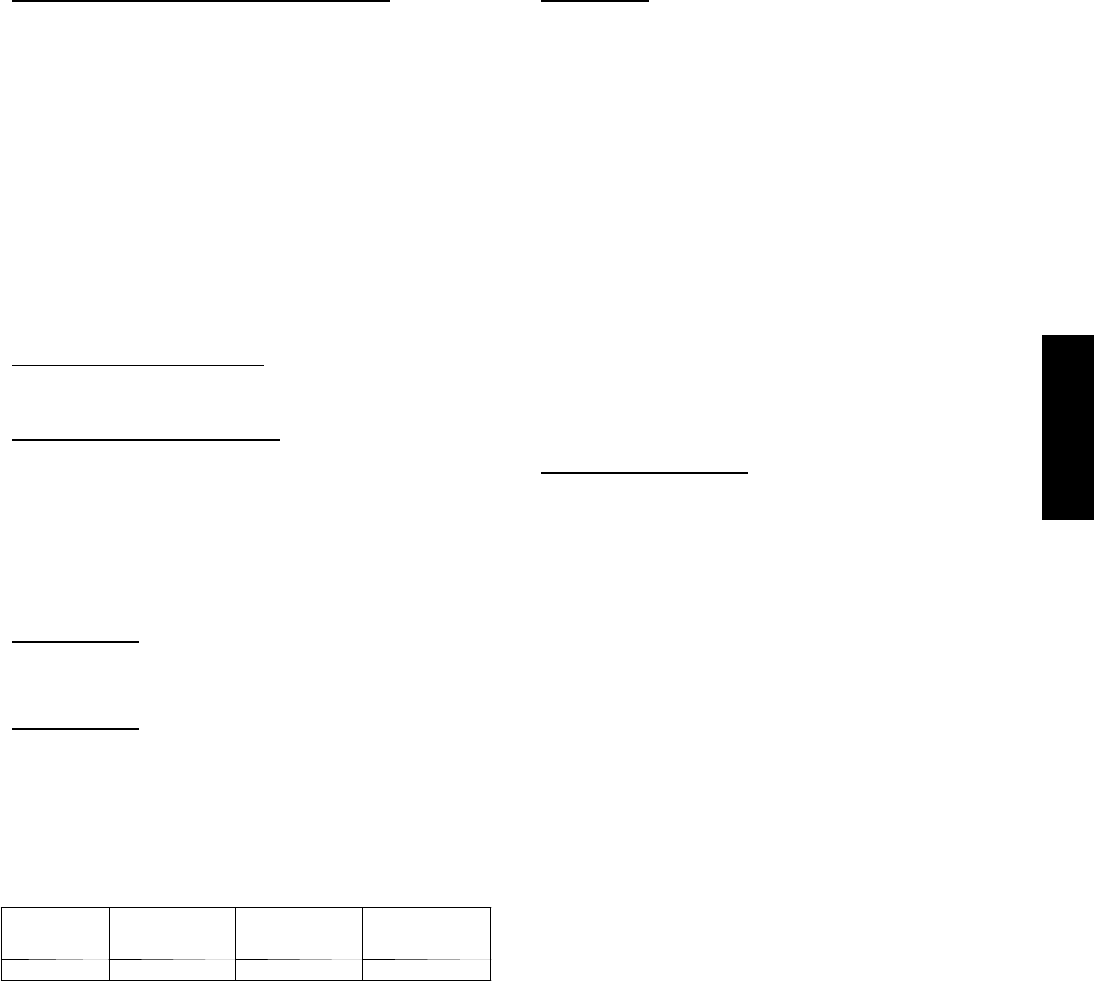
7
Communication and Status Function Lights
For Evolution Control only, Green communications (COMM)
Light
A green LED (COMM light) on the outdoor board (see Fig. 6)
indicates successful communication with the other system
products. The green LED will remain OFF until communication is
established. Once a valid command is received, the green LED will
turn ON continuously. If no communication is received within 2
minutes, the LED will be turned OFF until the next valid
communication.
Amber Status Light
An amber colored STATUS light is used to display the operation
mode and fault codes as specified in the troubleshooting section.
See Table 5 for codes and definitions.
NOTE: Only one code will be displayed on the outdoor unit
control board (the most recent, with the highest priority).
Crankcase Heater Operation
The crankcase heater is energized during off cycle below 65°F
(18.33°C).
Outdoor Fan Motor Operation
The outdoor unit control energizes the outdoor fan any time the
compressor is operating except for low--ambient cooling operation.
The outdoor fan remains energized if a pressure switch or
compressor overload should open. Outdoor fan motor will
continue to operate for one minute after the compressor shuts off
when the outdoor ambient is greater than or equal to 100_F
(37.78_C) to reduce pressure differential for easier starting on next
cycle.
On 286B models
-- The outdoor fan motor is a PSC type. A fan
relay on the control board turns the fan off and on by opening and
closing a high voltage circuit to the motor. It does not change
speeds between low and high stage operation.
On 289B models
-- The outdoor fan is an ECM type. The motor
control is continuously powered with high voltage. The motor
speed is determined by electrical pulses provided by the PWM
outputs on the control board. The ECM motor RPM adjusts to
outdoor conditions as described in Table 3. The PWM output can
be measured between the PWM1 and PWM2 terminals on the
circuit board with a volt meter set to DC volts.
Table 3 – Outdoor Fan Motor PWM
Outdoor Temp (DC volts, Tolerance +/-- 2%)
MODEL
LOW --- STAG E
(OAT≤104_F/40_C)
H IG H --- STAG E
(OAT≤104_F/40_C)
LOW --- &
HIGH---STAGE
(OAT>104_F/40_C)
289B036 9.06 10.23 11.90
NOTE:
For 289B models in low---ambient cooling, the PWM output for both high---
and low---stage equals the value for low---stage operation below 55_F
(12.8_C).
In low ambient cooling (below 55_F/12.78_C) on 286B and 289B
models, the control board cycles the fan off and on.
Time Delays
The unit time delays include:
S Five minute time delay to start cooling or heating operation
when there is a call from the thermostat or user interface. To
bypass this feature, momentarily short and release Forced
Defrost pins.
S Five minute compressor re--cycle delay on return from a
brown--out condition.
S Two minute time delay to return to standby operation from last
valid communication (with Evolution only).
S One minute time delay of outdoor fan at termination of cooling
mode when outdoor ambient is greater than or equal to 100_F
(37.78_C).
S Fifteen second delay at termination of defrost before the
auxiliary heat (W1) is de--energized.
S Twenty second delay at termination of defrost before the outdoor
fan is energized (unless fan delay defeated).
S Thirty second compressor delay when quiet shift enabled.
S There is no delay between staging from low to high and from
high to low capacity. The compressor will change from low to
high and from high to low capacity “on the fly” to meet the
demand.
Compressor Operation:
The basic scroll design has been modified with the addition of an
internal unloading mechanism that opens a by--pass port in the first
compression pocket, effectively reducing the displacement of the
scroll. The opening and closing of the by--pass port is controlled
by an internal electrically operated solenoid. The modulated scroll
uses a single step of unloading to go from full capacity to
approximately 67% capacity.
A single speed, high efficiency motor continues to run while the
scroll modulates between the two capacity steps. Modulation is
achieved by venting a portion of the gas in the first suction pocket
back to the low side of the compressor, thereby reducing the
effective displacement of the compressor.
Full capacity is achieved by blocking these vents, thus increasing
the displacement to 100%. A DC solenoid in the compressor
controlled by a rectified 24 volt AC signal in the external solenoid
plug moves the slider ring that covers and uncovers these vents.
The vent covers are arranged in such a manner that the compressor
operates at approximately 67% capacity when the solenoid is not
energized and 100% capacity when the solenoid is energized. The
loading and unloading of the two step scroll is done ”on the fly”
without shutting off the motor between steps.
NOTE: 67% compressor capacity translates to approximately
75% cooling or heating capacity at the indoor coil.
The compressor will always start unloaded and stay unloaded for
five seconds even when the thermostat is calling for high stage
capacity.
286B / 289B