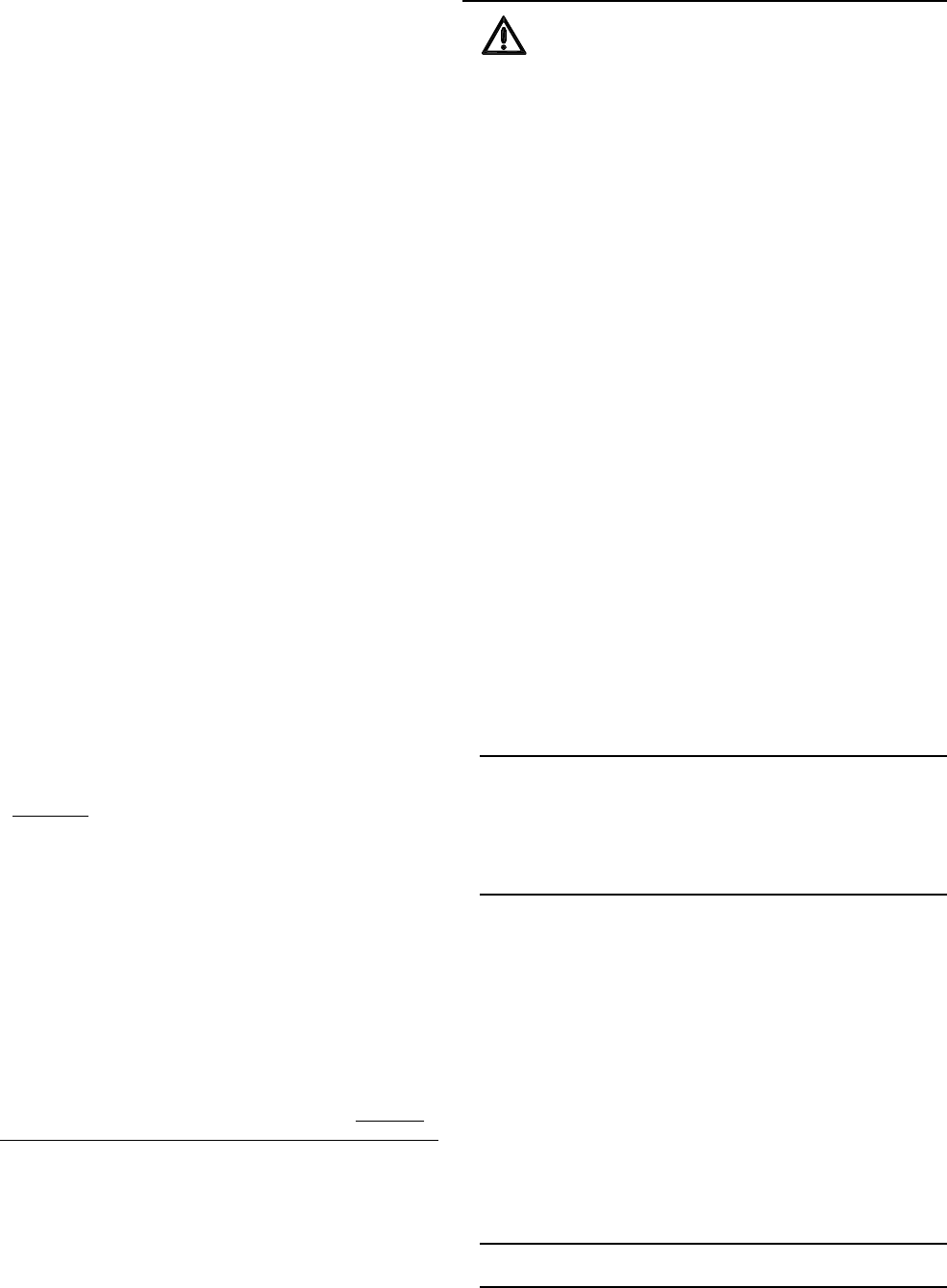
97
Unit Start-Up (Continued)
Full Modulating Gas Furnace
Full Modulating gas heaters are available for the 500, 850
and 1000 MBH heater sizes. These heaters are available in
the same cabinet sizes as the current heaters.
The firing rate of the unit can vary from the pilot rate of 125
MBH up to the nameplate rating of the unit. The turn down
ratios, therefore, vary from 4:1 for the 500 MBH to 8:1 for
the 1000 MBH heater.
Heat Exchanger
The heat exchanger drum, tubes and front and rear head-
ers are constructed from AL-6XN or 25-6MO, two of the
most corrosion resistant stainless steel alloys available.
Unit control
The unit is controlled by a supply air temperature sensor lo-
cated in the supply air stream for VAV units. CV units have
two sensors, one located in the supply air stream and the
zone sensor. The temperature sensor signal is sent to the
Heat module of the Intellipak
®
Unit Control. The control sig-
nal from the Heat Module is an inverse proportional 5 -10V
DC. The higher the voltage signal, the lower the call for
heat.
The 5 -10V DC. signal controls the angular position of the
combustion air damper through a direct coupled damper ac-
tuator motor. The position of the air damper in turn controls
the combustion air pressure that is sensed by the modulat-
ing gas valve. The greater the combustion air pressure, the
greater the call for gas and the higher the firing rate of the
heater. As the temperature setpoint is reached, the Modu-
lating Heat control will cause the combustion air actuator to
change the damper position to a lower firing rate that
matches the heat load of the space.
1. Use Table 4-1 to program the following system compo-
nents for operation by scrolling through the Human Inter-
face displays;
Gas Heat
Supply Fan (On)
Inlet Guide Vanes (100% Open, if applicable)
Variable Frequency Drive (100% Output, if
applicable)
RTM Occ/Unocc Output (Unoccupied)
High Fire (90%)
Turn the 115 volt control circuit switch 4S24
located in the heater control panel to the "On"
position.
Open the manual gas valve, located in the gas
heat section.
2. Once the configuration for the appropriate heating sys-
tem is complete, press the NEXT key until the LCD dis-
plays the “Start test in __Sec.” screen. Press the + key to
designate the delay before the test is to start. This ser-
vice test will begin after the TEST START key is pressed
and the delay designated in this step has elapsed. Press
the ENTER key to confirm this choice.
3. Press the TEST START key to start the test. Remember
that the delay designated in step 2 must elapse before
the system will begin to operate.
WARNING
Rotating Components!
During installation, testing, servicing and troubleshoot-
ing of this product it may be necessary to measure the
speed of rotating components. Have a qualified or li-
censed service individual who has been properly
trained in handling exposed rotating components, per-
form these tasks. Failure to follow all safety precau-
tions when exposed to rotating components could re-
sult in death or serious injury.
4. Once the system has started, check the appearance of
the flame through the sight glass provided on the front of
the heat exchanger. In appearance, a normal flame has
a clearly defined shape, and is primarily (75%) blue in
color with an orange tip.
5. Check the inlet gas pressure at the modulating gas valve.
The inlet pressure should be 6" to 8" w.c..
6. Use a carbon dioxide analyzer and measure the percent-
age of carbon dioxide in the flue gas. Refer to the illus-
tration in Figure 4-7. Take several samples to assure that
an accurate reading is obtained. If the measured carbon
dioxide level is between 8.0% and 9.5%, no adjustment
is necessary. If the CO
2
is outside this range, it indicates
incomplete combustion due to inadequate air or exces-
sive gas.
The pressure ratio and bias adjustment screws are lo-
cated on top of the regulator under a sealed plate. The
actual settings can be seen through windows on each
side of the regulator. Refer to the illustration in
Figure 4-9.
Note: The burner capacity is controlled by the
movement of the air damper. This has been preset
at the factory and normally does not need field
adjustment. The combustion quality (air/gas) is
controlled by the settings on the regulator (the plus
(+) and minus (-) indications relate to the change in
gas flow.
7. Set the air/gas ratio to the desired value using the #1 ad-
justment screw until the optimum values between (8.0
and 9.5%) are obtained (course setting).
8. Use Table 4-1 to program the minimum (5%) firing rate.
Allow the system to operate for approximately 10 min-
utes.
9. Use a carbon dioxide analyzer and measure the percent-
age of carbon dioxide in the flue gas. If the measured
carbon dioxide level is between 6.0% and 8.0%, no ad-
justment is necessary. If an adjustment is needed, turn
the #2 adjustment screw on the regulator in the Plus (+)
direction to increase the CO
2
and in the Minus (-) direc-
tion to decrease the CO
2
. Refer to the illustration in Fig-
ure 4-9 for the adjustment screw location.
Note: It is normal for the low fire CO
2
to be lower
than the high fire.