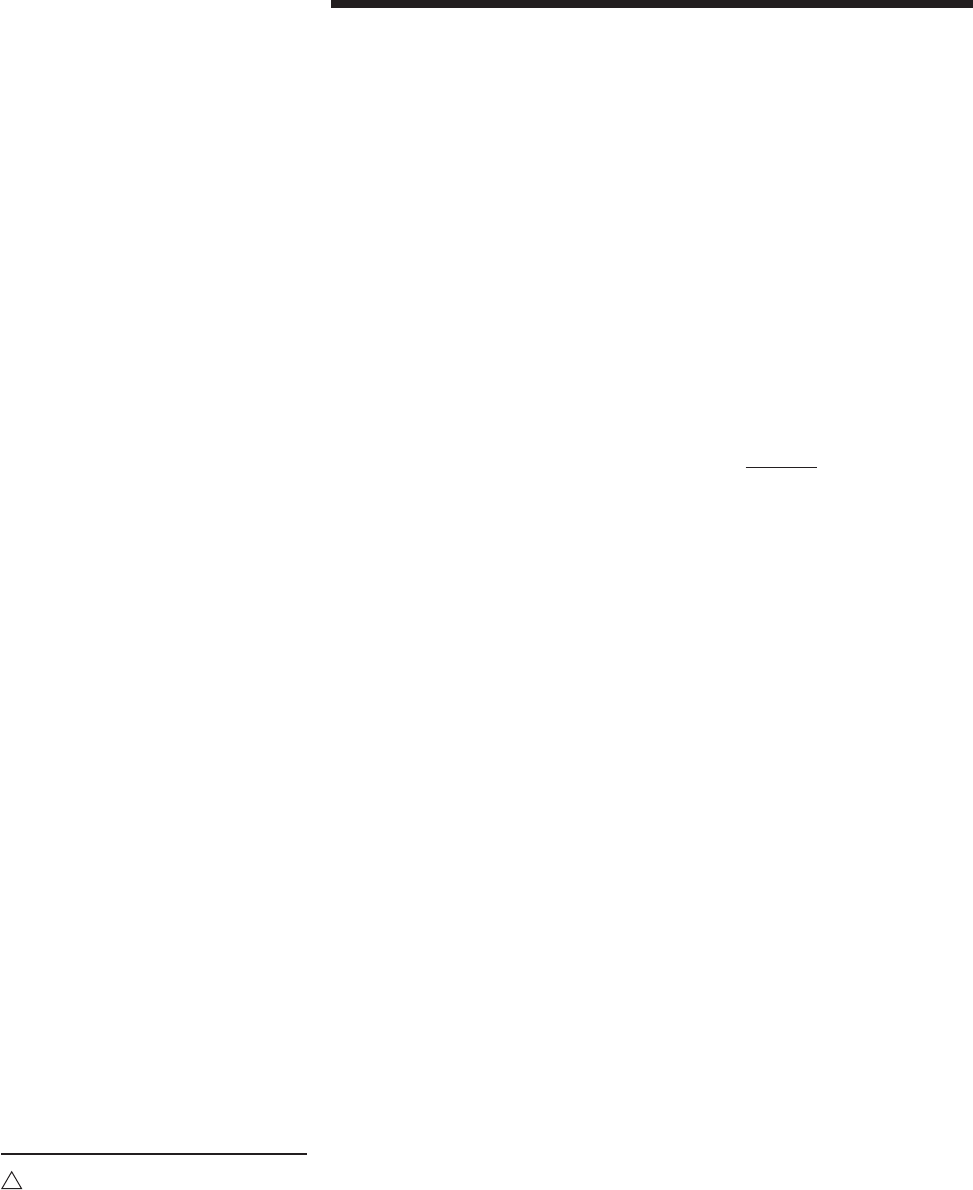
9
Operation
➠
Tower Performance
The following is intended to serve as a guideline for the operation of this
counterflow mechanical draft cooling tower. The owner may use this infor-
mation to develop preliminary operating procedures. As operational experi-
ence with the system accumulates, more definitive responses to specific
conditions will be developed by the owner’s operating personnel.
Keep the tower clean and the water distribution uniform to obtain continued
maximum cooling capacity. (See Caution note on page 15 and Warning
note on page 17.) Do not allow excessive deposits of scale or algae to
build up on the filling or eliminators. Keep the nozzles free of debris to
assure correct distribution and cooling of water. Uniform water distribution
over the entire fill plan area is vital to the efficient operation of a film-filled
cooling tower.
The capacity of a tower to cool water to a given cold water temperature
varies with the wet-bulb temperature and the heat load on the tower. As
the wet-bulb temperature drops, the cold water temperature also drops.
However, the cold water temperature does not drop as much as the wet-
bulb temperature. (Wet-bulb temperature is the temperature indicated
by the wet-bulb thermometer of a sling or mechanically aspirated
psychrometer.)
A tower does not control the heat load. For a given heat load, the quan-
tity of water circulated determines the cooling range. The hot and cold
water temperatures increase with higher heat loads. (Cooling range is
the temperature difference between the hot water coming into the
cooling tower and the cold water leaving the tower.)
Fan Drive
Air is caused to move through the tower by the operation of electric motor-
driven fans. At full speed, these fans are designed (and pitched) to move
the amount of air required to accomplish the design thermal performance.
Proper utilization of these fans provides the operator a means by which
to adjust the level of thermal performance to suit the requirements of the
load. (See Temperature Control and Energy Management on pages
13 and 14.)
If two-speed motors are used, allow a time delay of a minimum of
20 seconds after de-energizing the high speed winding and before
energizing the low speed winding. Tremendous stresses are placed
on driven machinery and motor unless the motor is allowed to slow
to low speed rpm or less before the low speed winding is energized.
▲ Caution