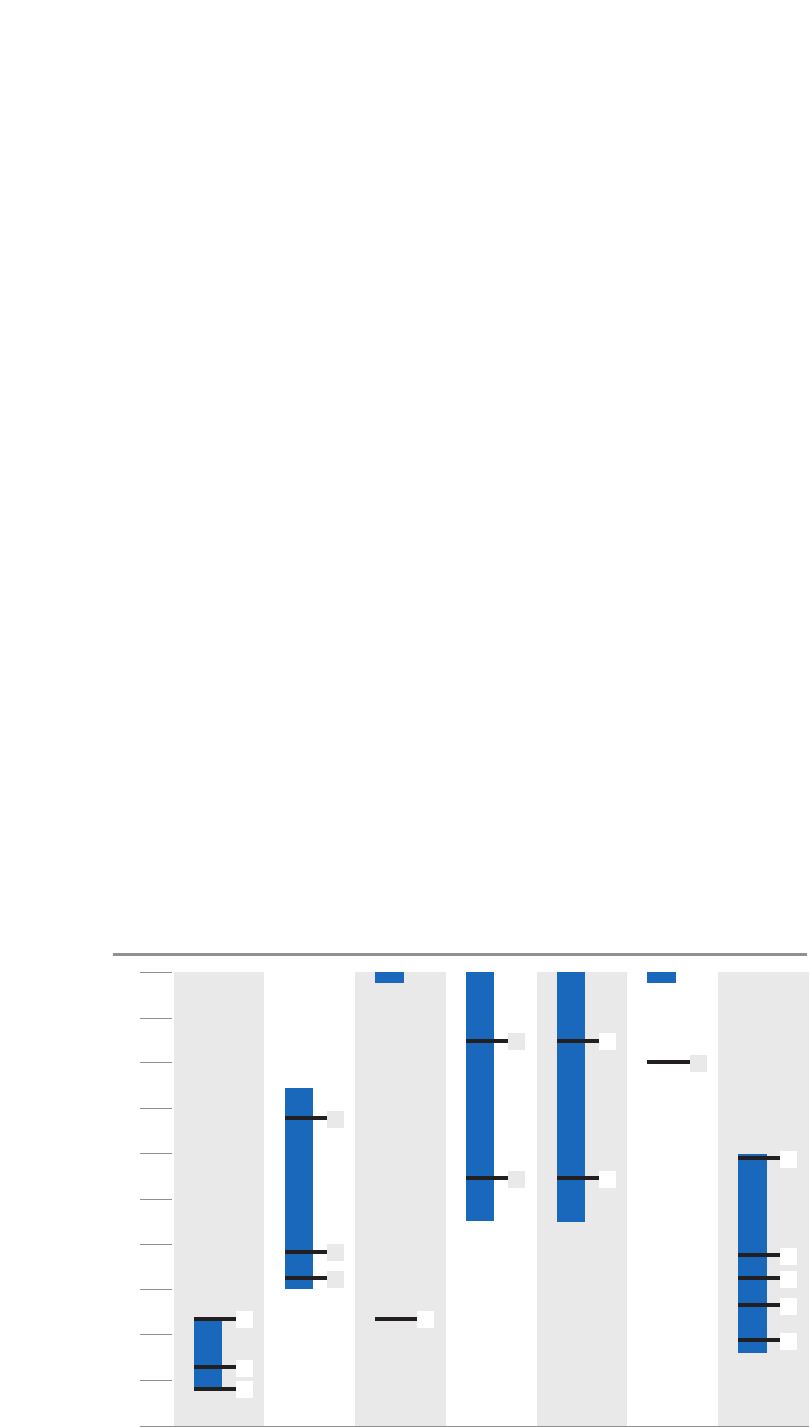
12
2
4
6
8
10
12
14
16
18
20
3
2
1
3
4
5
6
12
11
10
9
8
7
2
1
5
6
ightweight construction is an obvious
solution in the quest to cut fuel con-
sumption and harmful emissions. These
days, a wide range of lightweight options
exist: the first generation of aluminum bodies
produced during the nineties saw the steel
industry respond with a plethora of new steels
and processing techniques. Even magnesium
can now be obtained in something other than
for a medium-sized series (30 to 50,000
vehicles p. a.) of body components (materi-
al, finishing, ready for assembly, without
lacquer)
1 Stamped sheets with low waste
2 Drawn sheets with low waste
3 Sheets with high waste
4 Benchmark for magnesium sheet techno-
logy and hot shaping in one process
5 Large castings
6 Small castings
7 Straight sections with large cross-section
8 Section bent
9 Section stretch-bent
10 Section bent, IHPF
11 Section, stretch-bent, IHPF,intensive
machining
12 Carbon-fiber-reinforced plastics (CFK) -
IM and SMC benchmark (from 2008)
Specific costs (/kg)
COST-EFFICIENT LIGHTWEIGHT BODIES Environmental protection necessitates lower
fleet consumption, while tough competition requires strict cost management. Although light-
weight construction concepts are central to the former, they still tend to hinder the latter.
One effective remedy is the cost/weight optimization method developed by IVM Automotive.
cast form, and it is almost impossible to num-
ber all the different plastics and composites
currently in use.
At the moment, however, lightweight con-
struction is having problems establishing
itself in series production; strict cost manage-
ment by OEM facing an unfavorable mar-
ket environment would appear to leave little
scope for innovative production materials and
Lightweight doesn’t
have to be expensive
L
COMPARISON OF SPECIFIC COSTS
Sheet steel
shells
Aluminum
sheets
Magnesium
castings
Magnesium
sheets
CFK Aluminum
section
Aluminum
castings