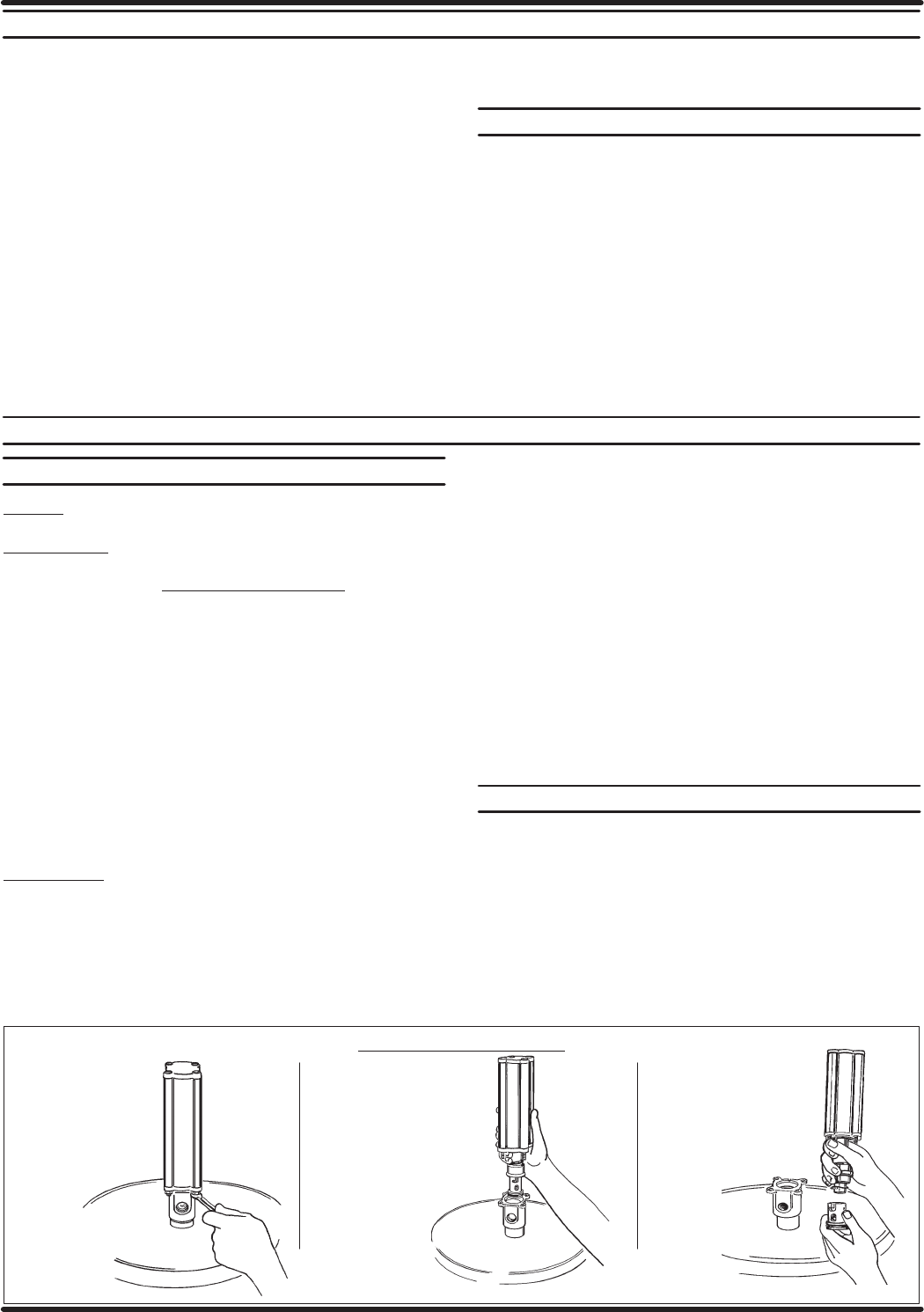
LM2203A-XPAGE4OF4
PLACING INT
O SER
VICE
AIR AND LUBRICATION REQUIREMENTS
Filtered air will help extend the life of the pump, allowing the pump to
operate moreefficiently andyield longerservice lifetomovingpartsand
mechanisms.
• Install an air line filter to provide good quality clean and dry air.
Install it up stream from the regulator.
• Use anairregulator ontheair supplytocontrol thepump cyclerate.
Install the regulator as close as possible to the pump.
• In most installations, lubrication is not required. If the pump needs
to have lubrication, install an air line lubricator and supply it with a
good grade of non-detergent oil or other lubricant compatible with
Buna -Nseals and setat arate notto exceedone drop perminute.
INSTALLATION
• Mount and secure the pump as required for the application.
• Attach a ground wire from the pump ground screw to a suitable
ground.
• Connect a fluid hose to the pump outlet. In most cases a pipe
sealant should be used on thread connection. Tighten all fittings.
Use caution not to damage threads.
OPERATION
START-UP
1. Turn the air regulator to ``0'' pressure setting.
2. Immerse the lower pump end into the material.
3. Open the dispensing device.
4. Start the pump cycling slowly by raising the pressure to 20 - 30
p.s.i. (1.4 - 2.1 bar).
5. Close the dispensing device. Allow the pump tostall and build line
pressure. Checkforany leaksandtightenfittingsasneeded.Adjust
pressure as required for the application.
SHUTDOWN
• Disconnect the air supply from the pump if it is to be inactive for a
few hours. Open the dispensing device to relieve line pressure.
SERVICE
PUMP
DISASSEMBL
Y / REASSEMBL
Y
NOTICE: The unique design of this pump allows for quick basic pump
service without total removal from the drum (refer to the views below).
DISASSEMBLY - All threads are right hand. Refer to figure 2.
These procedures are for the installation of repair kit parts. DisĆ
connect air supplyand relieveall system pressureprior toservicĆ
ing. Carefully remove the parts, inspect parts for damage, nicks or
excessive wear and determine if any parts will need replacement.
Follow the threedisassembly steps inthe detail viewsbelow and place
the pump on a clean bench.
1. Remove (1) bolts. Remove (18) packing, (17) bushing and (16) ``O"
ring.
2. Grasp the (11) cylinder and remove the (20,14) piston assembly.
3. Remove (15)lower capand (3)trackgasket. Remove(12) retaining
ring, then pull (14) piston off (20) piston rod.
4. Remove (2) cap and (3)track gasket. Push on thelarge o.d.end of
the (7) spool to remove the (4) sleeve. Grab the nose of (7) spool
and pull out. Repeat for other sleeve and spool.
5. Remove (36) adapter, releasing (10) muffler housing.
REASSEMBLY - Thoroughly clean and lubricate all seals with
Shell Darina ``EP" 2.Replace allsoft partswithnew onesincluded
in the repair kit.
Note: Refer to the illustration (Fig 2) for ``U" cup lip seal direction.
1. Replace the seals on both the (7) spools and (4) sleeves.
2. Locate the valve chamber on the (11) cylinder where the 3/8'' dia.
hole islocated andinstall oneofthe (4)sleeves. Insertthe(7) spool
from the opposite end. Next, install the remaining sleeve and spool.
3. Replace the (3) track gasket and install (2) cap.
4. Replacethe (13)piston ``U"cups (referto figure2for properorientaĆ
tion). Replacethe(19) ``O"ring andassemble(14)pistonto(20) pisĆ
ton rod and retain with (12) retaining ring.
5. Install the (20,14) piston assembly using greatcare to collapsethe
outer lip of the second ``U" cup, allowing it to slip into the cylinder.
6. Replace the(3) trackgasket and installthe (15)cap. Installthe (16)
``O" ringonto thepiston rod, replace(17) bushing and(18) packing.
7. Replace the (25) ``O" ring and re-attach the (24) inner check.
8. Slide thepump assemblyback intothe (26)base /lowerpump secĆ
tion. Press the sections together and align the air inlet and pump
outlet as requiredand replace thefour (1)bolts and (27)nuts (tightĆ
en to 80 in. lbs (9 Nm).
TROUBLE SHOOTING
If the pump will not cycle or will not deliver material.
• Be certain to check for non-pump problems including kinked, reĆ
strictive or plugged inlet/outlet hose or dispensing device. DepresĆ
surize thepump systemand cleanout anyobstructionsin theinlet /
outlet material lines.
• Check all seals, including track gaskets.
• Check direction of ``U" cup lips.
C) Unlock the(24) inner
check fromthe pistonrod.
FIGURE5
FIGURE4
B) Graspthe lower motor
cap andpull outthe motor
and uppersectionof the
lowersection.
PUMP DISASSEMBLY DETAIL
FIGURE3
A) Removethefour
nuts fromthebase of
the AirMotor.
PN97999-678