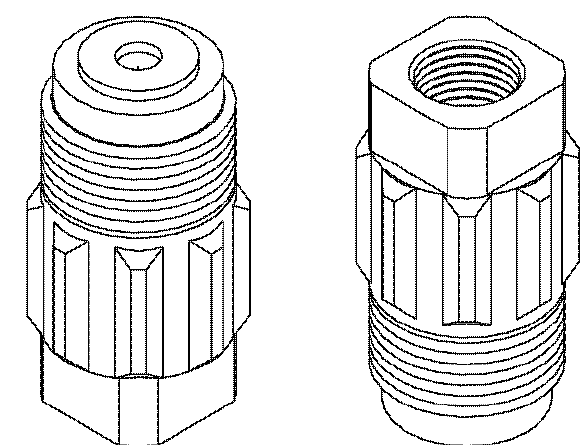
12
7.3 Check Valves
7.3.1 General Description
Most fluid metering problems are related to check valves. Problems usually stem from solids
accumulation between valve and seat, corrosion of seating surfaces, erosion, or physical damage due
to wear or the presence of foreign objects.
The valve incorporates a ball, guide, and seat. Flow in the unchecked direction lifts the ball off the
seat, allowing liquid to pass through the guide. Reverse flow forces the ball down, sealing it against
the sharp edge of the seat. The guide permits the ball to rotate but restricts vertical and lateral
movement in order to minimize “slip” or reverse flow. Ball rotation prolongs life by distributing
wear over the entire surface of the ball. Since ball return is by gravity, the valve must be in the
vertical position in order to function properly. Parts are sealed by “O”-rings.
All OMNI models with the exception of the DC5 and 6 in metal construction utilize a convenient
cartridge-type check valve. All check components are pre-assembled and the cartridge should be
replaced as a unit. When replacing, note that valves are marked with the flow direction, as the suction
and discharge configurations are different.
OMNI DC5 and 6 models supplied with metal (316ss) reagent head construction utilize a multi-part
check valve assembly, secured to the reagent head with a tie-bar clamping arrangement. These utilize
the same components (seat, ball, and guide) and operate in the same manner as the cartridge type.
Figure 9, check valves, DC2
Figure 9, check valves DC2
Check Valve
Suction Position
Check Valve
Discharge Position