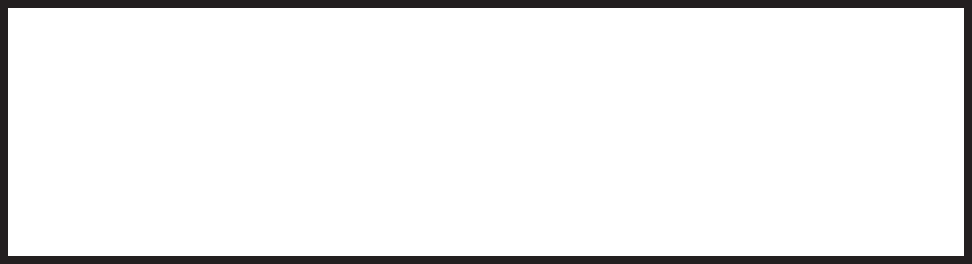
20
C. Assembly of Crown 60/100mm Concentric Venting
(IMPORTANT - Skip to Section D for 80/125mm Concentric Vent Assembly)
WARNING
Failure to follow the instructions could result in fl ue gas leakage into the combustion air or indoor
air, resulting in unsafe or unreliable operation.
• Do not lubricate concentric gaskets with anything other than water.
• Do not attempt to cut any piping except as permitted in this section. When cutting these
sections, make sure all cuts are square and allow for proper insertion.
• Do not attempt to try to mix this concentric pipe with other venting systems.
Concentric vent components supplied with the boiler are packed in a separate carton and include the following:1)
60/100mm elbow adaptor (Crown PNa) 340509).
60/100mm terminal section (straight section with a terminal and overall length of 27 3/4” (Crown PN 230520).b)
Two (2) Rubber wall grommets (Crown PN c) 230522).
Vent gasket and screws for attachment of vent system to boiler. d)
The 82mm air inlet orifi ce required for Vent Option 1 is packed in the boiler carton.
The 60/100 straight adaptor is optional equipment. It is supplied with the same screws and gasket as the 60/100
elbow adaptor.
Start by attaching the elbow adaptor (or straight adaptor, if used instead) to the top of the boiler using the gasket 2)
and four 4.2mm sheet metal screws provided in the vent kit as shown in
Figure 7.20. For V
Figure 7.20. For Vent Option 1, install the
82mm air inlet orifi ce as shown.
If no additional sections of concentric pipe are required, attach the terminal section to the elbow. In most cases, it 3)
will need to be cut before doing so. Use the following procedure to cut the pipe:
Measure distance “L” from the outside surface of the exterior wall to the end of the elbow as shown in Figure a)
7.21.
Add 2-1/8” to distance “L”. Carefully mark this length on the pipe as shown in Figure 7.22.b)
Press in the two tabs holding the plastic terminal in the terminal section (Figure 7.22). Carefully pull out the c)
terminal and the inner pipe.
Cut the d) outer pipe only at the point marked in Step (b) using aviation shears, a hacksaw, or an abrasive
wheel cutter. Be careful to cut the pipe square. De burr the cut end with a fi le or emery cloth.
Cut the plastic inner pipe so that it will protrude 3/8” beyond the outer pipe when reinstalled in the terminal e)
section (Figure 7.23). Use a fi ne tooth hacksaw or a PVC saw to cut the plastic pipe and be careful to cut the
pipe square. De burr the cut edge of the plastic pipe with a fi le, razor blade, or fi ne sandpaper.
Reinstall the inner pipe in the terminal section. Slip the outside wall grommet over the terminal section and f)
position so that it covers the joint between the outer pipe and the terminal (Figure 7.24).
Make a mark on the terminal section 1” from the cut end of the outer pipe as shown in Figure 7.24.g)
Pass the terminal section through the wall from the outside. Push the remaining wall grommet over the h)
terminal section on the inside of the wall. Push the terminal section into the elbow until the mark made in Step
(g) is no longer visible. If necessary, the brown gasket in the inner pipe may be lubricated with a few drops of
water.
The terminal section must be attached to the elbow with a single #10 x 1/2” sheet metal screw ( not supplied) i)
at the top of the elbow. Drill a 1/8” hole in the location shown in Figure 7.25. Use a short drill bit or a drill
stop to ensure that the drill bit does not penetrate the pipe by more than 3/8”. Install a #10 x 1/2” screw
in this hole. Do not use a screw longer than 1/2” long.
If not already done, make sure that both wall grommets are fi rmly against the interior and exterior wall j)
surfaces. Seal any cracks or other openings near the terminal through which exhaust could enter the building.