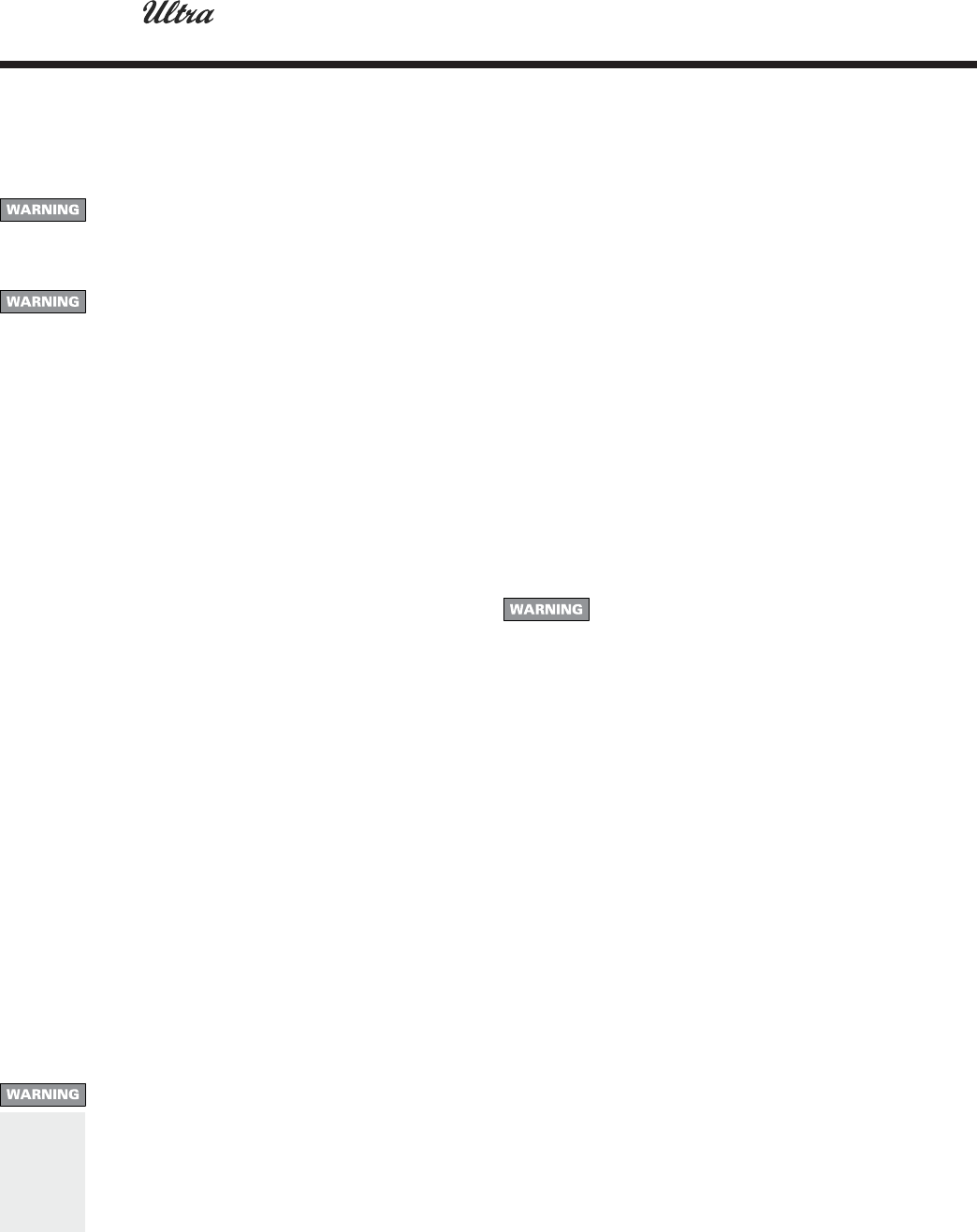
GAS-FIRED WATER BOILER SERIES 2 — Boiler Manual
Part number 550-100-026/0404
23
Startup
6
Check/control water chemistry
Do not use petroleum-based cleaning or sealing
compounds in boiler system. Damage to elastomer
seals and gaskets in system could occur, resulting in
substantial property damage.
Before filling the boiler and system with water, verify
the following. Failure to comply could result in boiler
failure or unreliable operation.
Water pH between 7.0 and 8.5
1. Maintain boiler water pH between 7.0 and 8.5. Check with
litmus paper or have chemically analyzed by water treatment
company.
2. If pH differs from above, consult local water treatment
company for treatment needed.
Hardness less than 7 grains
1. Consult local water treatment companies for unusually hard
water areas (above 7 grains hardness).
Chlorine concentration less than 200 ppm
1. Filling with chlorinated fresh water should be acceptable since
drinking water chlorine levels are typically less than 5 ppm.
2. Do not use the boiler to directly heat swimming pool or spa
water.
3. Do not fill boiler or operate with water containing chlorine in
excess of 200 ppm.
Clean system to remove sediment
1. You must thoroughly flush the system (without boiler
connected) to remove sediment. The high-efficiency heat
exchanger can be damaged by buildup or corrosion due to
sediment.
2. For zoned systems, flush each zone separately through a purge
valve. (If purge valves and isolation valves are not already
installed, install them to properly clean the system.)
3. Flush system until water runs clean and you are sure piping is
free of sediment.
Test/replace freeze protection fluid
1. For systems using freeze protection fluids, follow guidelines in
Ultra Boiler Freeze Protection Supplement.
Fill and test water system
1. Fill system only after ensuring the water meets the requirements
of this manual.
2. Close manual and automatic air vents and boiler drain valve.
3. Fill to correct system pressure. Correct pressure will vary with
each application.
a. Typical cold water fill pressure for a residential system is 12 psi.
b. Pressure will rise when boiler is turned on and system water
temperature increases. Operating pressure must never exceed 25 psig.
4. At initial fill and during boiler startup and testing, check system
thoroughly for any leaks. Repair all leaks before proceeding
further.
Eliminate all system leaks. Continual fresh make-up
water will reduce boiler life. Minerals can build up in
sections, reducing heat transfer, overheating heat
exchanger, and causing heat exchanger failure.
5. The system may have residual substances that could affect
water chemistry. After the system has been filled and leak tested,
verify water pH and chlorine concentrations are acceptable.
Freeze protection (when used)
NEVER use automotive or standard glycol antifreeze,
even glycol made for hydronic systems. Use only
freeze-protection fluids recommended in the Ultra
Boiler Freeze Protection Supplement. Follow all
guidelines in the Freeze Protection Supplement, and
thoroughly clean and flush any replacement boiler
system that has used glycol before installing the new
Ultra boiler.
1. Determine freeze protection fluid quantity using total system
water content, following fluid manufacturers’s instructions.
Boiler water content is listed on page 43. Remember to include
expansion tank water content.
2. Local codes may require back flow preventer or actual
disconnect from city water supply.
3. When using freeze protection fluid with automatic fill, install a
water meter to monitor water make-up. Freeze protection fluid
may leak before the water begins to leak, causing concentration
to drop, reducing the freeze protection level.
Purge air from water system
1. Purge air from system:
a. Connect a hose to the purge valve (see purge/drain valves, item 11,
in piping diagrams on pages 15 through 18. Route hose to an area
where water can drain and be seen.
b. Close the boiler or system isolation valve between the purge valve
and fill connection to the system.
c. Close zone isolation valves.
d. Open quick-fill valve on cold water make-up line.
e. Open purge valve.
f. One zone at a time, open the isolation valves. Allow water to run
through the zone, pushing out the air. Run until no noticeable air
flow is present. Close the zone isolation valves and proceed with the
next zone. Follow this procedure until all zones are purged.
g. Close the quick-fill water valve and purge valve and remove the
hose. Open all isolation valves. Watch that system pressure rises to
correct cold-fill pressure.
h. After the system has operated for a while, eliminate any residual air
by using the manual air vents located throughout the system.
i. If purge valves are not installed in system, open manual air vents in
system one at a time, beginning with lowest floor. Close vent when
water squirts out. Repeat with remaining vents.
2. Open automatic air vent (diaphragm-type or bladder-type
expansion tank systems only) one turn.
3. Open other vents:
a. Starting on the lowest floor, open air vents one at a time until water
squirts out.
b. Repeat with remaining vents.
4. Refill to correct pressure.