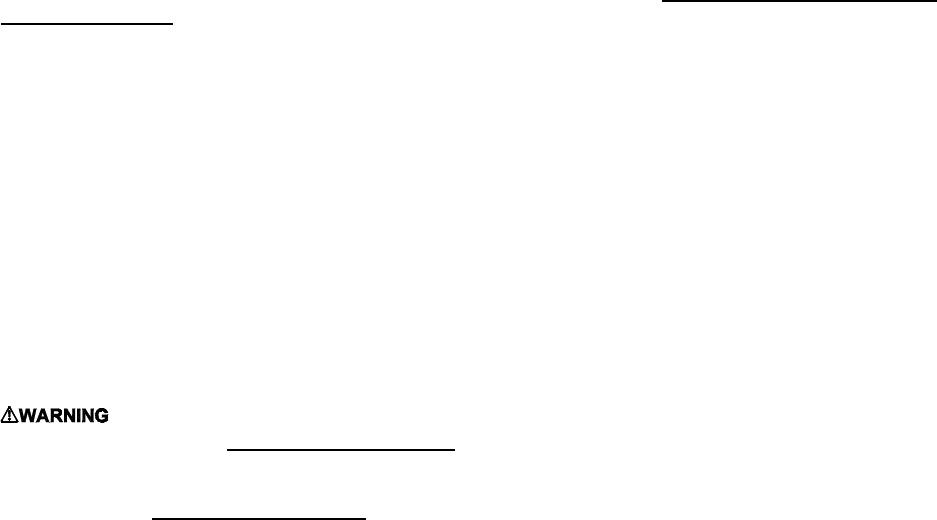
23
the pump. Pitching the line upward toward the tank will help prevent the formation of air pockets in the
line.
NOTICE: An oil safety valve or a delayed-action, solenoid valve should be
installed in the oil supply line of all gravity-fed systems.
When the oil tank is located below the level of the burner, it is necessary to “lift” the oil to the burner. A
return line should be connected between the fuel pump and tank. This requires insertion of the "by-pass"
plug into the fuel pump. If the lift (vertical distance between the supply line inlet and the burner) exceeds
approximately 8 feet, a two-stage pump should be installed with a return line. When a return line is used
with either single or two-stage pumps, in-line air is automatically returned to the tank, making the oil pump
and lines self-purging.
Underground tanks should be located outside the building. Installation of above ground tanks is permitted
inside buildings, under certain conditions, as well as outside. Consult the Standard for Installation of Oil-
Burning Equipment for restrictions. If permitted, connect the burner oil supply line near the base of the
tank, opposite of the fill end. Connection at this point tends to flush older oil through and out of the tank.
This helps to prevent the accumulation of rainwater and condensed water vapor in the tank, which can
cause the tank to corrode.
If the oil supplier does not already use oil additives, it is recommended that additives be used to emulsify
any water accumulation in the oil.
J. OIL FILTER:
It is strongly recommended that an oil filter assembly be installed in the oil supply line to the unit. This
filter should have the capacity to trap a 40-50 micron particle.
The filter cartridge should be replaced at least once a year. The filter body should be thoroughly cleaned
before installing a new cartridge.
K. ELECTRICAL WIRIING:
: This appliance must be grounded in accordance with local codes, or in the absence
of local codes, with the National Electrical Code
, ANSI/NFPA 70-1999, or the latest edition.
All wiring must conform to the provisions of local codes or, in the absence of local codes, with the
provisions of the National Electrical Code
, ANSI/NFPA 70-1999, or the latest edition, and this instruction
manual.
This appliance requires 120 VAC, 60 Hz, single-phase power. Refer to Table 10 for typical electrical
current draws of the individual appliance motors, recommended sizes for over-current and short circuit
devices, and minimum recommended field wiring sizes. Electrical service must be brought to the unit from
a circuit breaker, or fused disconnect switch, in accordance with local codes. The disconnecting switch
must be located reasonably close to and within sight of the unit. Care must be taken to ensure correct
polarity when wiring the furnace.
Two-wire service, one “hot” lead (L1) and a common (L2), plus a ground conductor, is required. Connect
power to the appliance control system at the junction box in the burner compartment. (A knockout fitting is
provided on the exterior of the burner compartment for this purpose.) A ground wire must be connected to
the grounding wire in the junction box.
Field wiring of power circuits to the appliance should consist of copper conductors rated for at least
15 amp service with an insulation temperature rating of at least 75°C temperature rise. Depending upon
code requirements, rigid or flexible conduit is recommended, and may be required. Connect the electric
power supply as shown in the wiring diagram located on the inside of the front door.