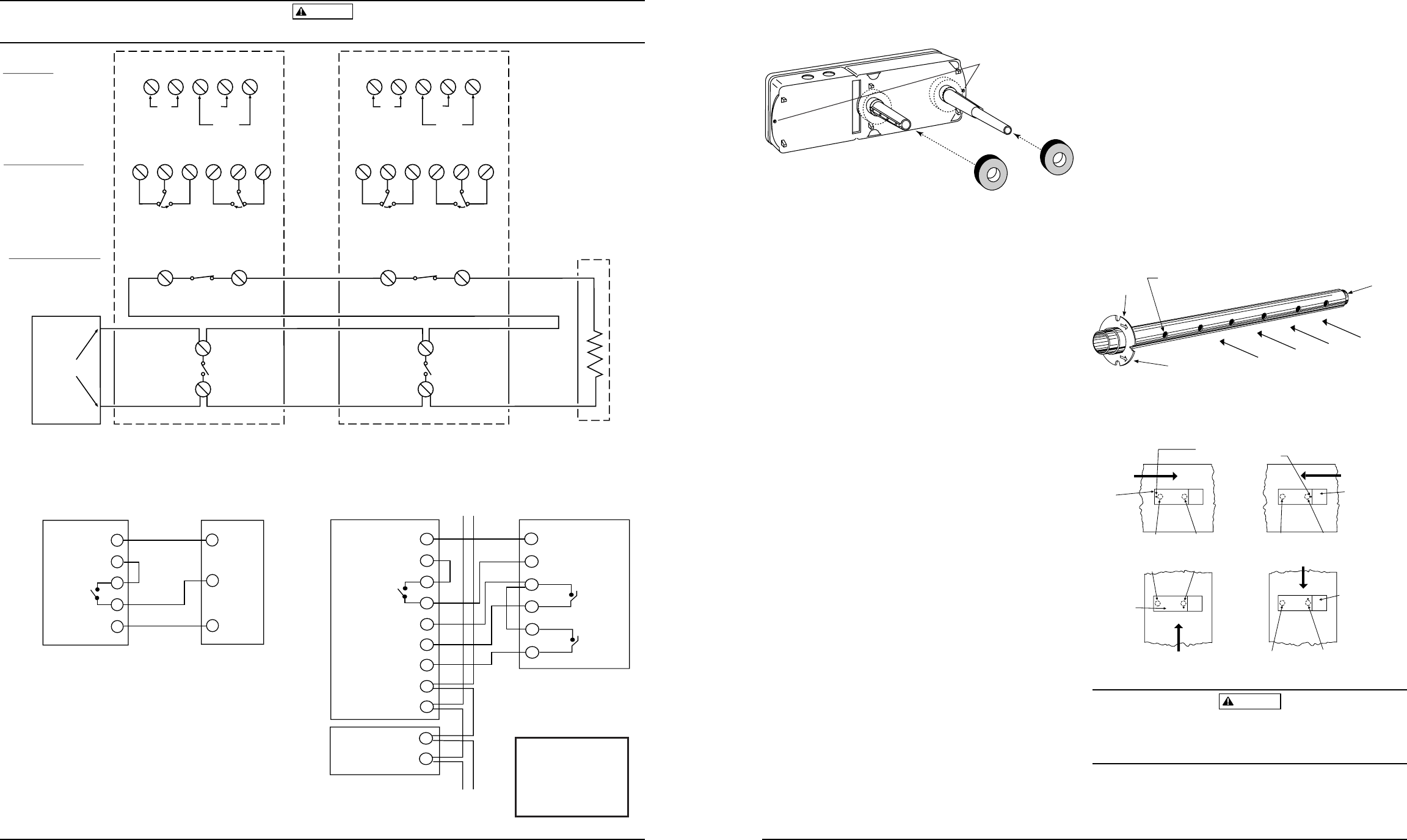
housing to the duct.
CAUTION: Do not overtighten the screws.
Figure 3. Installation of foam gaskets over sampling
tube bushings:
A78-2045-00
[5.4] Sampling Tube Installation for Ducts Greater
Than 1
1
/2 Feet Wide
The sampling tube is identified by a series of air inlet holes
on the tube. A telescoping tube is included for ducts up to
18″ in width. All other lengths must be purchased sepa-
rately. Order the correct length, as specified in Table 1, for
width of the duct where it will be installed. The exhaust
tube is molded onto the base of the duct housing, and the
A2440-00 Exhaust Tube Extension is available as an acces-
sory in those cases where the molded exhaust port does not
extend at least 2 inches into the duct.
The inlet tube is always installed with the air inlet holes
facing into the air flow. To assist proper installation, the
tube’s mounting flange is marked with arrows. Make sure
the inlet tube is mounted so that the arrows point into the
air flow (see Figure 4). Figure 5 shows the various combi-
nations of tube mounting configurations with respect to air
flow. Mounting the detector housing in a vertical orienta-
tion is acceptable, provided that the air flows directly into
the sampling tube holes as indicated in Figure 4.
Table 1. Inlet tubes required for different duct
widths:
Outside Duct Width Inlet Tube Required
1 to 2 ft. ST-1.5
2 to 4 ft. ST-3
4 to 8 ft. ST-5
8 to 12 ft. ST-10
[5.4.1] Installation For Ducts Greater Than 1
1
/2 Feet
But Less Than 8 Feet Wide
1. If the tube is longer than the width of the air duct, drill a
3
/4″ hole in the duct opposite the hole already cut for the
inlet tube. Make sure the hole is 1″ to 2″ below the inlet
hole on the opposite side of the duct to allow moisture
drainage away from the detector. If the tube is shorter than
the width of the air duct, install the end plug into the inlet
tube as shown in Figure 4. Sampling tubes over 3 ft. long
must be supported at the end opposite the duct detector.
2. Slide the tube into the housing bushing that meets the
air flow first. Position the tube so that the arrows point
into the air flow.
3. Secure the tube flange to the housing bushing with two
#6 self-tapping screws.
4. For tubes longer than the width of the air duct, the tube
should extend out of the opposite side of the duct. If
there are more than 2 holes in the section of the tube ex-
tending out of the duct, select a different length using
Table 1. Otherwise, trim the end of the tube protruding
through the duct so that 1″ to 2″ of the tube extend out-
side the duct. Plug this end with the end plug and tape
closed any holes in the protruding section of the tube. Be
sure to seal the duct where the tube protrudes.
Figure 4. Air duct detector inlet sampling tube:
A78-2047-00
Figure 5. Tube mounting configurations with varying
air flow direction:
AIR FLOW
DIRECTION
DUCT
DETECTOR
HOUSING
DOTS INDICATE POSITION OF
SAMPLING TUBE HOLES
AIR FLOW
DIRECTION
DUCT
DETECTOR
HOUSING
INLET
TUBE
EXHAUST
TUBE
AIR FLOW
DIRECTION
EXHAUST
TUBE
INLET
TUBE
INLET
TUBE
EXHAUST
TUBE
DUCT
DETECTOR
HOUSING
AIR FLOW
DIRECTION
EXHAUST
TUBE
INLET
TUBE
DUCT
DETECTOR
HOUSING
A.
B.
C.
D.
NOTE: Orientations C and D apply only to metal sampling tubes.
WARNING
In no case should more than 2 air inlet holes be cut off the
tube. There must be a minimum of 10 holes in the tube ex-
posed to the air stream.
[5.4.2] Installation For Ducts More Than 8 Feet Wide
NOTE: To install inlet tubes in ducts more than 8 feet wide,
D100-68-00 3 I56-1147-07
SCREW HOLES FOR
ATTACHING HOUSING
TO DUCT WORK.
INLET
TUBE
END
PLUG
AIR HOLES
ARROWS
MUST FACE
INTO AIR FLOW
AIR FLOW DIRECTION
FLANGE
D100-68-00 6 I56-1147-07
24V
120
VAC
220/240
VAC
910ABC
AVAILABLE POWER INPUTS
ALARM AUXILIARY CONTACTS
FOR FAN SHUTDOWN, ETC.
16 6 17
7188
N.C.C.N.O.N.O.C.N.C.
ALARM AUXILIARY CONTACTS SHOWN IN
STANDBY. CONTACTS TRANSFER DURING
ALARM AS INDICATED BY THE ARROWS.
SUPERVISORY TROUBLE CONTACTS
TROUBLE CONTACTS CLOSED IN ALARM AND STANDBY.
CONTACTS OPEN WHILE DETECTOR HEAD OR POWER IS
REMOVED OR WHEN TAMPER FEATURE TIMES OUT. OPEN
CONTACTS SIGNAL TROUBLE CONDITION TO PANEL.
24V
220/240
VAC
910ABC
AVAILABLE POWER INPUTS
ALARM AUXILIARY CONTACTS
FOR FAN SHUTDOWN, ETC.
16 6 17
7188
N.C.C.N.O.N.O.C.N.C.
ALARM AUXILIARY CONTACTS SHOWN IN
STANDBY. CONTACTS TRANSFER DURING
ALARM AS INDICATED BY THE ARROWS.
SUPERVISORY TROUBLE CONTACTS
TROUBLE CONTACTS CLOSED IN ALARM AND STANDBY.
CONTACTS OPEN WHILE DETECTOR HEAD OR POWER IS
REMOVED OR WHEN TAMPER FEATURE TIMES OUT. OPEN
CONTACTS SIGNAL TROUBLE CONDITION TO PANEL.
314 314
4
5
ALARM
INITIATION
CONTACTS
CONTACTS SHOWN
OPEN IN STANDBY.
CONTACTS CLOSE
IN ALARM.
4
5
ALARM
INITIATION
CONTACTS
CONTACTS SHOWN
OPEN IN STANDBY.
CONTACTS CLOSE
IN ALARM.
ALARM
INITIATION
LOOP
UL LISTED 4-WIRE
CONTROL PANEL
FIRST DETECTOR IN THE LOOP
DH100ACDC
LAST DETECTOR IN THE LOOP
DH100ACDC
EOL RESISTOR
SPECIFIED BY
PANEL MANUFACTURER
CONNECT POWER SOURCE
TO APPROPRIATE TERMINALS
OF EACH DETECTOR. SEE
SPECIFICATIONS FOR
ADDITIONAL POWER SUPPLY
INFORMATION.
FOR WIRING OF AUXILIARY
DEVICES, REFER TO
MANUFACTURER’S
INSTALLATION INSTRUCTIONS
OR CONTACT MANUFACTURER.
NOTE: THE SUPERVISORY RELAY NOW
PROVIDES A "FORM C" CONTACT FOR
CUSTOMIZED APPLICATIONS.
FOR STANDARD APPLICATIONS, ONLY
THE "NO" CONTACT IS USED
POWER INPUTS ACCEPT
24 VDC, 24 VAC 50-60 HZ,
120 VAC 50-60 HZ, OR
220/240 VAC 50-60 HZ.
CONNECT POWER SOURCE
TO APPROPRIATE TERMINALS
OF EACH DETECTOR.
AUX. CONTACT RATINGS
10A @ 30 VDC RESISTIVE
10A @ 250 VAC
100mA MINIMUM @ 5 VDC
NOT INTENDED FOR
CONNECTION TO CONTROL
PANELS.
TROUBLE CONTACT RATING
2.0 A @ 30 VDC resistive
+
—
120
VAC
CAUTION
Do not loop wire under terminals when wiring detectors. Break wire runs to provide system supervision of connections.
Figure 8. Wiring diagram for DH100ACDC to APA451:
A78-2352-03
Figure 7. System wiring diagram for 4-wire duct smoke detectors (detectors powered from initiating circuit):
15
19
14
3
20
1
3
2
Alarm Signal
Aux. Power +
Sup. N. O.
Sup. COM
Aux. Power –
NOTE: Wiring diagram shown is for DH100ACDC 4-wire duct
smoke detector system equipped without a control panel.
Alarm
Power
Common
APA451DH100ACDC
15
19
14
3
20
2
11
2
6
1
Alarm Signal
Aux. Power +
Sup. N. O.
Sup. COM
Aux. Power –
Reset
Test
(Red LED) Alarm
(Green LED) Power
Common
12
1
12
1
Interconnect +
Interconnect –
DH100ACDC
DH100ACDC
RTS451KEY
5
4
3
Reset
Common
Test
NOTE: Wiring diagram shown is for
DH100ACDC 4-wire duct smoke
detector system equipped
without a control panel.
Figure 9. Wiring diagram for DH100ACDC to
RTS451KEY and interconnect feature:
Unit Two
IMPORTANT!
ALL INTERCONNECTED
UNITS MUST BE POWERED
BY THE SAME,
INDEPENDENT POWER
SUPPLY.