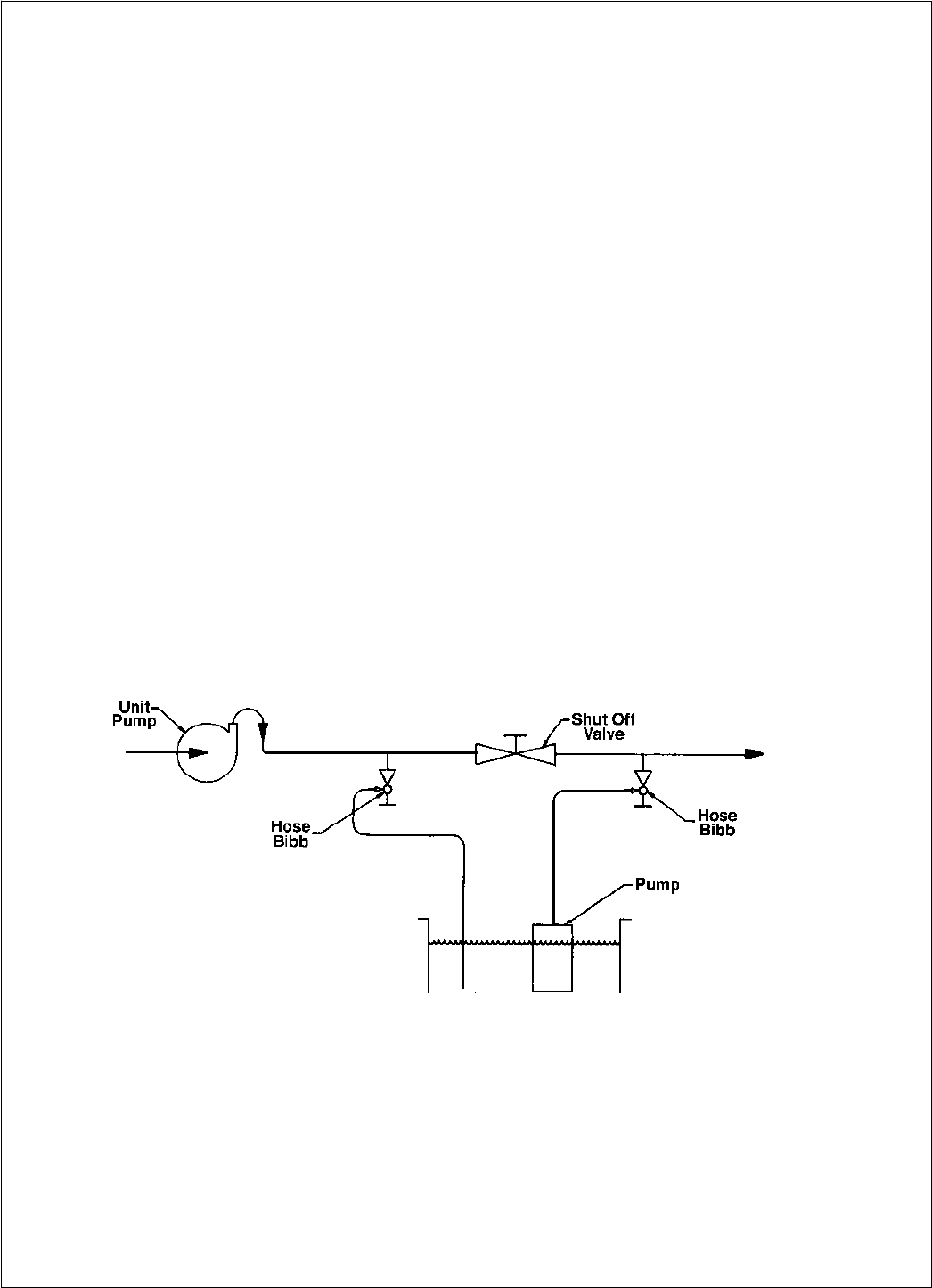
Start-up
1. Prestart:
Check for correct dry cooler fan rotation. This can be done
by quickly jogging the fan contactor. Be sure that the fans
run freely. The same check is recommended for pumps.
2. Filling and Purging the System
The system should be pressure tested before adding glycol.
The system can be tested with air or water, however if the
ambient temperature is at or below freezing the use of air
is recommended. Test pressure should not exceed 60
PSIG.
a. Roof Mounted Fluid Cooler
To fill the system, pour the premixed water and glycol
into the expansion tank. Fill the system until the
expansion tank is half full, then purge the air from
ALL vents. Operate the system for a minute, then
purge ALL vents again, and add glycol as required.
Repeat the purging of all vents after the first hour of
operation and again after several hours of operation.
b. Ground Mounted Fluid Cooler
The fluid cooler may be lowest point in the system,
consequently the premixed water and glycol will have
to be pumped into the system. Close the shut off valve
and open the two hose bibbs installed in the piping
run on the leaving side of the pump, see piping
diagram.
Connect a pump and hose to the hose bibb away
from the pump and a hose to the hose bibb closest
to the pump. Begin pumping the glycol mixture into
the system at FULL PRESSURE. For the return
hose you should close the hose bibb so that you
get only a small flow of fluid or air. This is
necessary so you will build a head of fluid which will
force the air from the system. Once all the air is out
you will have a steady flow of only fluid. At this joint
you should close off the two hose bibbs and open
the shut off valve. See Diagram 3.
3. Flow Adjustment Procedure:
Once the system is completely full of fluid, start the fluid
circulating pump. To assure proper fluid flow, adjust the
shut-off valve for required GPM by checking pump curve
and observing gauge pressure, or by using an in-line flow
meter.
4. Instruction Envelope:
Keep wiring diagrams, instructions, list of spare parts, in
an envelope within easy reach of the installed dry cooler.
Diagram 3.
Space and Location Requirements
The most important consideration which must be taken
into account when deciding upon the location of air-cooled
equipment is the provision for a supply of ambient air to the
condenser, and removal of heated air from the fluid cooler
area. Where this essential requirement is not adhered to, it
will result in higher head pressures, which cause poor operation
and possible eventual failure of equipment. Units must not be
located in the vicinity of steam, hot air or fume exhausts.
Another consideration which must be taken is that the
unit should be mounted away from noise sensitive spaces
and must have adequate support to avoid vibration and noise
transmission into the building. Units should be mounted over
corridors, utility areas, rest rooms and other auxiliary areas
where high levels of sound are not an important factor. Sound
and structural consultants should be retained for
recommendations.
9