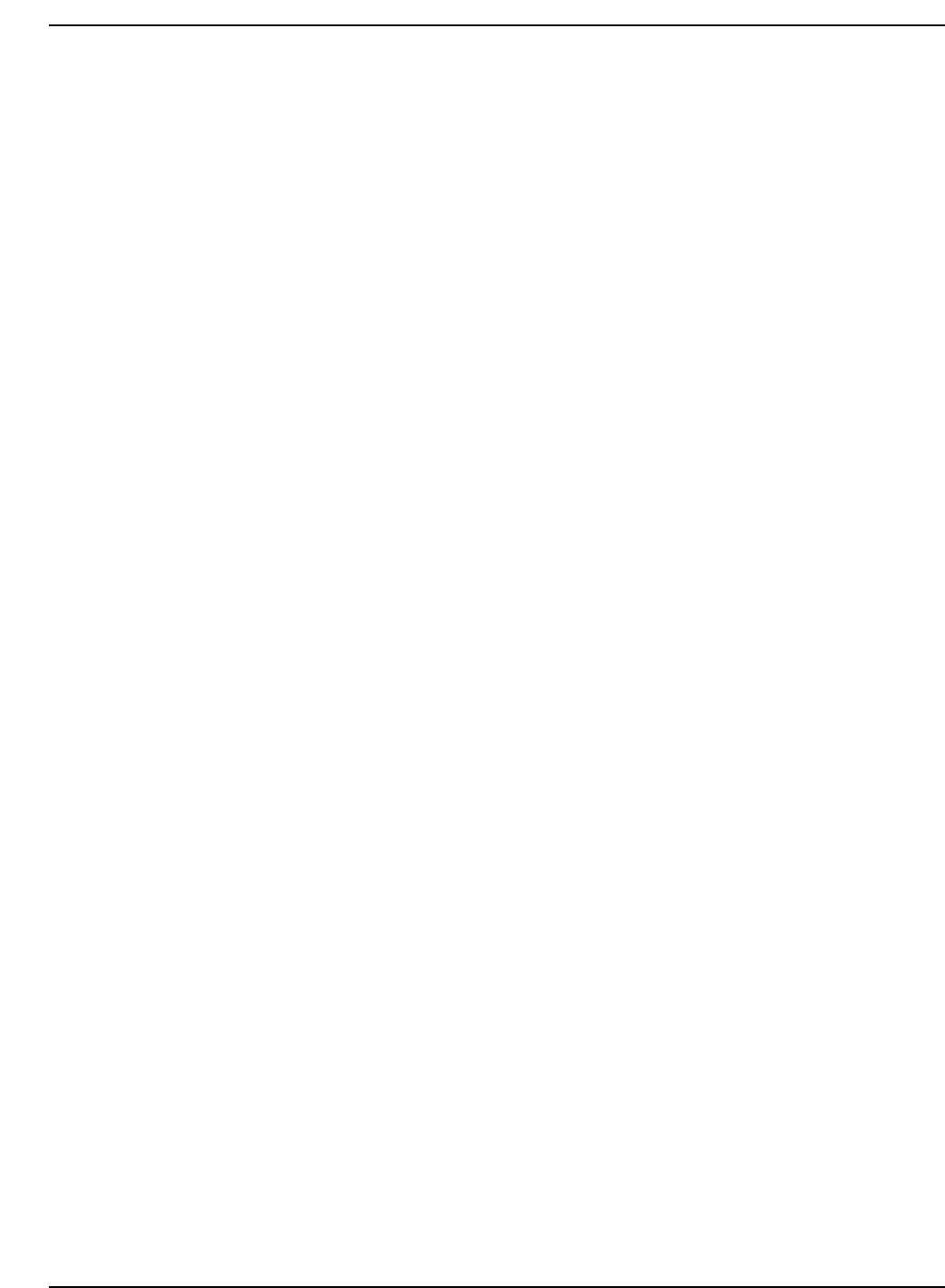
38
37. 24 VAC is now sent to the pressure switch (P.S.)
terminal on ignition modules 1 and 2.
38. Once the pressure switch signal is received at
ignition module 1, hot surface igniter 1 is ener-
gized by a 120 VAC signal from S-1 on ignition
module 1. (The hot surface igniter must draw
greater than 3.1 amps while being energized or
ignition lockout will occur after three tries.)
39. Once ignition module 1 determines that hot sur-
face igniter 1 has heated up and operating proper-
ly, a 24 VAC signal is output from pin GV on mod-
ule 1.
40. 24 VAC signal is received at gas valve 1 thus ener-
gizing it.
41. The stage 1 LED on the diagnostics display board
is now illuminated.
42. The coil of relay K-2 is now energized with the (K-
2) contacts closing downstream of the stage 2
connections and upstream of the stage 3 connec-
tions.
43. The gas coming through the burners should ignite
from the heat of hot surface igniter 1 and the flame
should carry over from one burner to the other
burners of stage 1. The remote sensor is now try-
ing to sense the flame. If the flame is not sensed
within 4 seconds, the ignition module will shut
down the gas valve and retry the hot surface ignit-
er. During ignition retry the heater must perform a
15-second pre-purge and an approximately 30-
second igniter warm-up before opening gas valve
1 again. The standard ignition module will attempt
ignition a maximum of three times prior to ignition
lockout.
44. As gas valve 1 opens and flame rectification is
received, time delay relay 1 (TD1) starts a 5-sec-
ond countdown.
45. After the 5 second countdown from TD-1, 24 VAC
is waiting at pin 3 of the stage 2 connection on the
CPW board.
46. The temperature controller closes the stage 2 con-
tacts and gas valve 2 in energized.
47. The stage 2 LED on the diagnostics display board
is now illuminated.
48. The temperature controller closes the stage 3 con-
tacts at J-3 on the CPW board.
49. Power is applied to the “TH” terminal of ignition
module 2.
50. Once the “TH” signal is received at ignition module
2, the hot surface igniter 2 is energized by a 120
VAC signal from S-1 on ignition module 2. (The hot
surface igniter must draw greater than 3.1 amps
while being energized or ignition lockout will occur
after three tries.)
51. Once ignition module 2 determines the hot surface
igniter is operating properly, a 24 VAC signal is
sent to energize gas valve 3.
52. The stage 3 LED on the diagnostics display board
is now illuminated.
53. Remote flame sensor 2 is trying to rectify.
54. The coil of relay K-5 (N.O.) is now energized with
the (K-5) contacts closing downstream of the
stage 4 connections.
55. Power is now applied to time delay relay 3 and the
contacts of TD-3 close after 5 seconds.
56. The stage 4 controller contacts close.
57. Power is applied to gas valve 4.
58. The stage 4 LED on the diagnostics display board
is now illuminated.
59. The heater is operating at full fire.
Models 2002A – 2342A
1. The black (hot) wire lead goes directly to the main
power switch. This black toggle switch is located
at the middle front of the control compartment.
2. When the main power switch is placed in the “ON”
position, 120 VAC is applied to the 120 VAC termi-
nal block on the circuit board and the 120/24 VAC
transformer is powered.
3. 120 VAC is waiting at the N.O. contacts of the
Economaster II pump delay.
4. Terminals L1 and F1 of the ignition module 1 are
powered with 120VAC.
5. 120 VAC power is also applied to the control
power connector on the circuit board.