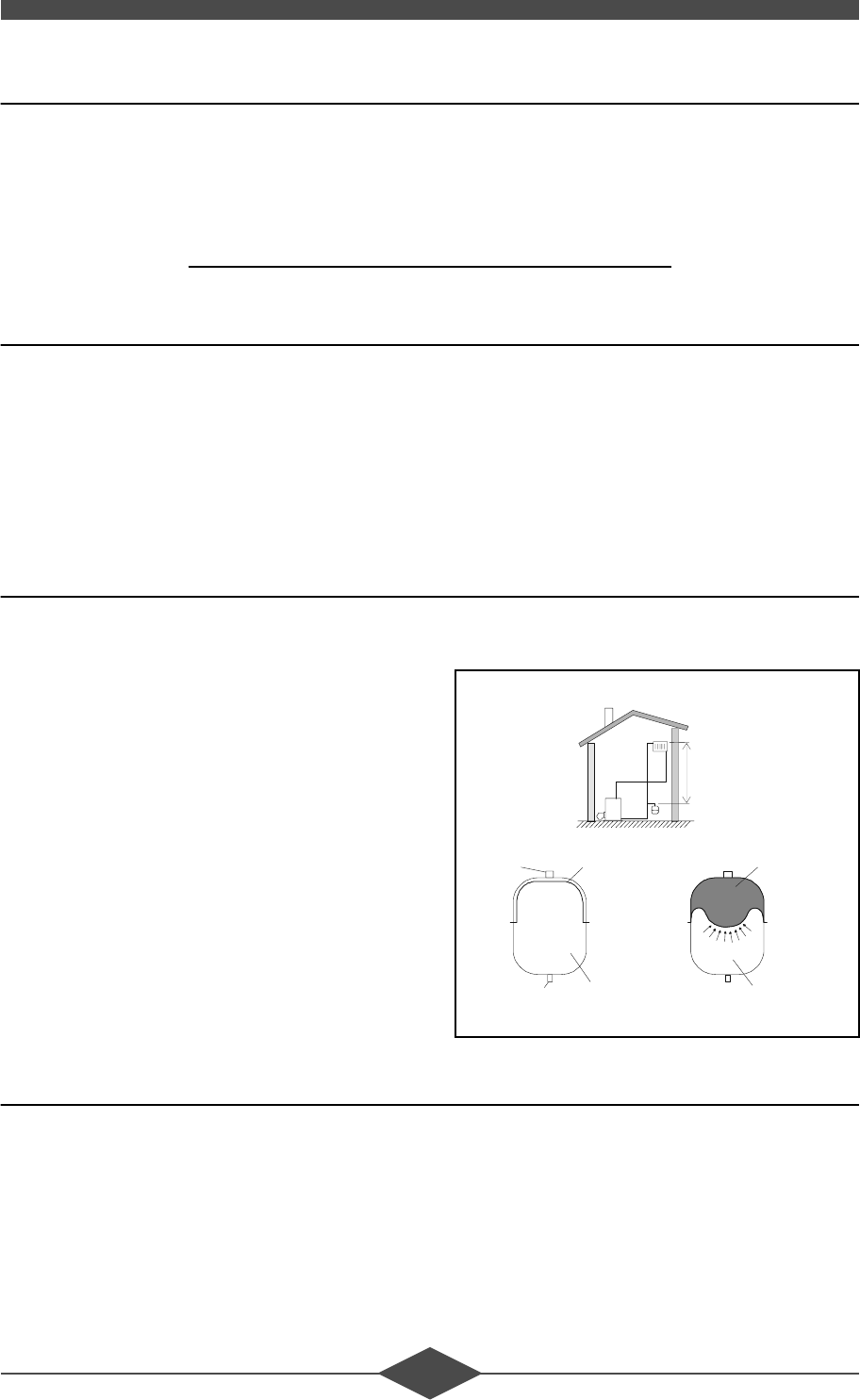
0$,17(1$1&(
%851(50$,17(1$1&(
Once adjusted properly, regular maintenance of the
oil burner is not generally required. A routine exami-
nation of the burner should include examination of
the burner fan and nozzle for dirt and the spark elec-
trodes for proper clearances. Replace the fuel filter
if necessary. Cleaning and adjustment is always ap-
propriate during periodic inspection.
If burner firing rate adjustment is required, follow
instructions in "Adjusting the Oil Burner".
$/:$<6&+(&.)25$1'&255(&7$1<)8(//($.6
$'',7,21$/&20321(170$,17(1$1&(
Check to see that the safety and regulation devices
(safety relief valve, air bleed valve, control box com-
ponents, etc.) are operating properly. Check also to
see that the condensate drain siphon is clean. If ne-
cessary, remove the bottom of the siphon, clean it,
replace it and then refill the siphon it with water. Also
check to see that neither the installation nor the boi-
ler have any water or fuel leaks (leaks may produce
a risk for safety and shorten the lifespan). If it beco-
mes frequently necessary to add water to maintain
pressure in the installation, even though no leaks
have been discovered, perform an expansion tank
check.
(;3$16,217$1.35(,1)/$7,2135(6685(&+(&.
Reduce the pressure in the heating installation by
opening the drain cock or the safety valve until the
pressure gauge reading is less than 7 - 8 psig (0.5
bar)
Check the pressure in the expansion tank and if ne-
cessary bring it back up to pressure. Replace the
tank if the membrane is punctured (water present in
the inflating valve)
To optimize the efficiency of the expansion tank:
• Adjust its pre-inflation pressure in line with the
installation. The pressure must correspond to
the static height of the installation (H), the
height between the highest point of the
installation and the expansion tank, as
expressed in bars where 10 meters in height =
1 bar.
• Adjust the filling pressure of the installation to
a value greater than 3 psig (0.2 bar) above the
pre-inflation pressure of the tank after totally
bleeding any air from the installation.
&20%867,21352'8&7)/8(
Examine the flue/combustion air system for leaks
and obstructions. Leaks can generally be detected
by the appearance of condensate stains on the out-
side of the pipes. Replace any damaged seals if ne-
cessary. The flue/combustion air pipe can be
cleaned with running water, if necessary, providing
that the water flow is not too great to be drained
through the condensate drain system. Leave the ex-
cess water in the condensate trap when cleaning is
completed.
H
Water inlet
Dilated water
volume
Inflating valve
Pressure rises as the
air is compressed
Max vessel
volume
Membrane