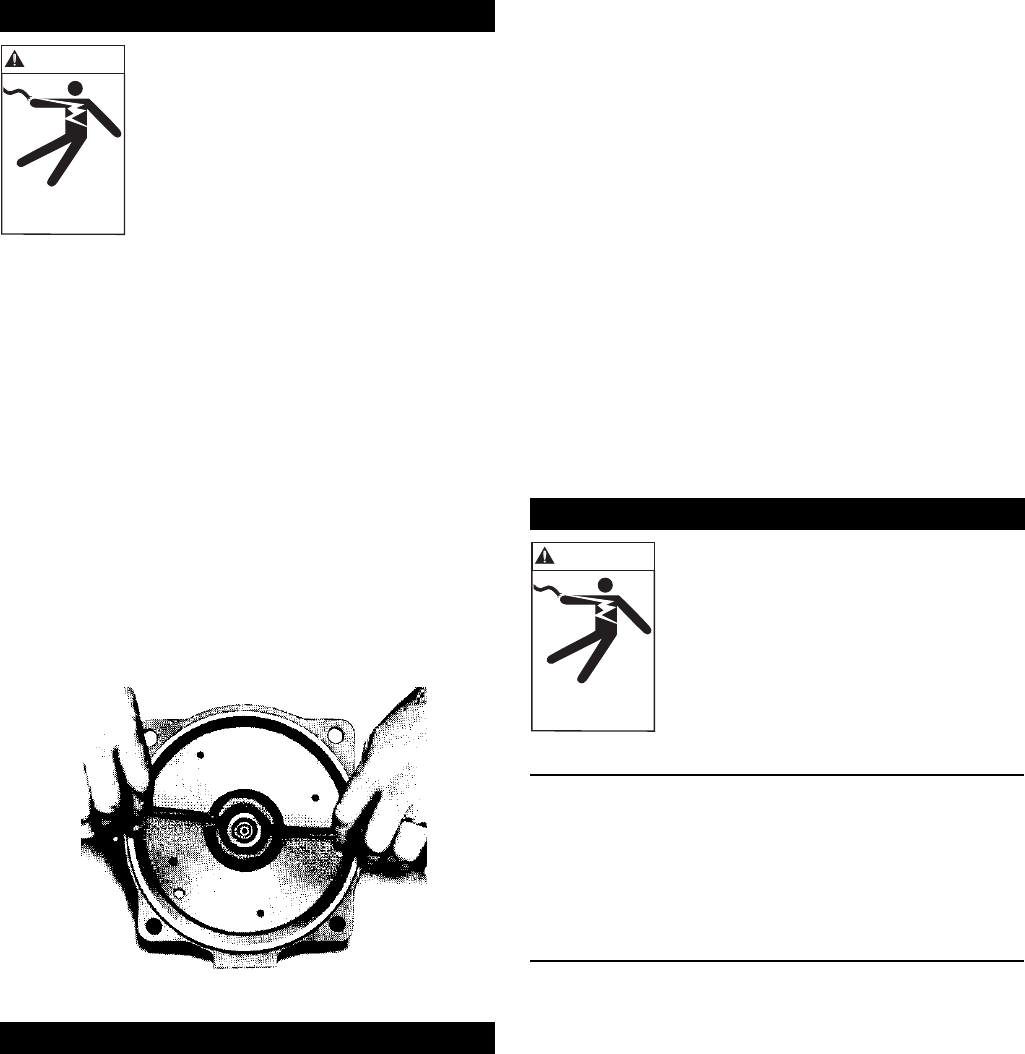
4
WARNING
Hazardous voltage
can shock, burn or
cause death.
WARNING
Hazardous voltage
can shock, burn or
cause death.
Disassembly
FAILURE TO DISCONNECT
ELECTRICAL POWER BEFORE
ATTEMPTING ANY MAINTENANCE
CAN CAUSE SHOCK, BURNS OR
DEATH.
1. Remove foot bolt (10).
2. Remove casing bolts (12).
3. Remove back pull-out assembly from casing (2).
4. Remove diffuser seal ring (3) and diaphragm (4).
5. Remove diffuser screws (5) from adapter (11).
6. Remove motor end plug or cover.
7. Restrain motor shaft from rotation by utilization of
the screwdriver slot, or
7
⁄16" shaft flats, accessible at the
motor shaft end.
8. Remove impeller (7), turning COUNTER-
CLOCKWISE.
9. Using two screwdrivers, pry off rotary section of
mechanical seal (8). Discard. See Figure 2.
10. Remove motor adapter bolts (12) and remove motor
adapter from motor.
11. Push stationary seat of mechanical seal out of
motor adapter. Discard seal seat.
Figure 2
Reassembly
• Clean and inspect all parts before reassembly.
1. Inspect seal seat bore for wear and debris, clean and
replace as necessary.
NOTICE: MECHANICAL SEAL MUST BE REPLACED
WHENEVER SEAL HAS BEEN REMOVED.
FOLLOW SEAL MANUFACTURER’S
INSTRUCTIONS CAREFULLY.
2. If necessary, seat ring may be lubricated with water or
glycerin to aid in installation. DO NOT contaminate
the seal face. Fully and squarely install the stationary
seat into the adapter. With a clean, lint free cloth,
CAREFULLY wipe the seat face clean of debris. DO
NOT damage the seal seat face.
3. Reinstall the motor adapter on the motor, making sure
that the motor shaft does not dislocate or damage the
stationary seal seat.
4. Fully and squarely install the seal rotary assembly
against the stationary seat. Be sure rotating seal face
does not drop out of holding collar and DO NOT
damage seal face.
5. On three phase units, impeller MUST be installed with
LOCTITE
®
“Purple”. Hold shaft from rotating, as
explained in the “DISASSEMBLY” section of the
manual, and install impeller by turning CLOCKWISE
until tight against motor shaft shoulder.
6. Replace diffuser. Align to prevent impeller rub.
7. Install new diaphragm and new diffuser seal ring.
8. Install motor and liquid end into casing.
9. Check impeller for binding by rotating the motor shaft.
If binding occurs, loosen casing bolts, readjust diffuser
until impeller hub turns freely. Retighten casing bolts in
a crossing pattern.
10. Replace all drain plugs and motor end components.
11. Reprime and operate according to instructions in the
“OPERATION” section of this manual.
Trouble Shooting
FAILURE TO DISCONNECT
ELECTRICAL POWER BEFORE
ATTEMPTING ANY MAINTENANCE
CAN CAUSE SHOCK, BURNS OR
DEATH.
SYMPTOM
Motor Not Running:
See Probable Causes 1 through 5.
Little or No Water Delivered:
See Probable Causes 3, 4, 6 through 12, 15.
Excessive Noise and Vibration:
See Probable Causes 3, 6, 7, 10, 12, 13, 14.
PROBABLE CAUSES
1. Motor thermal protector tripped.
2. Open circuit breaker or blown fuse.
3. Impeller binding.
4. Motor improperly wired.
5. Defective motor.
6. Pump is not primed, air or gases in pumpage.
7. Discharge, suction plugged or valve closed.
8. Incorrect rotation. (3 phase only)
9. Low voltage or phase loss.
10. Impeller worn or plugged.
11. System head too high.
12. NPSHA too low – excessive suction lift or loss.
13. Discharge head too low – excessive flow rates.
14. Pump, motor or piping loose.
15. End of suction piping not submerged.