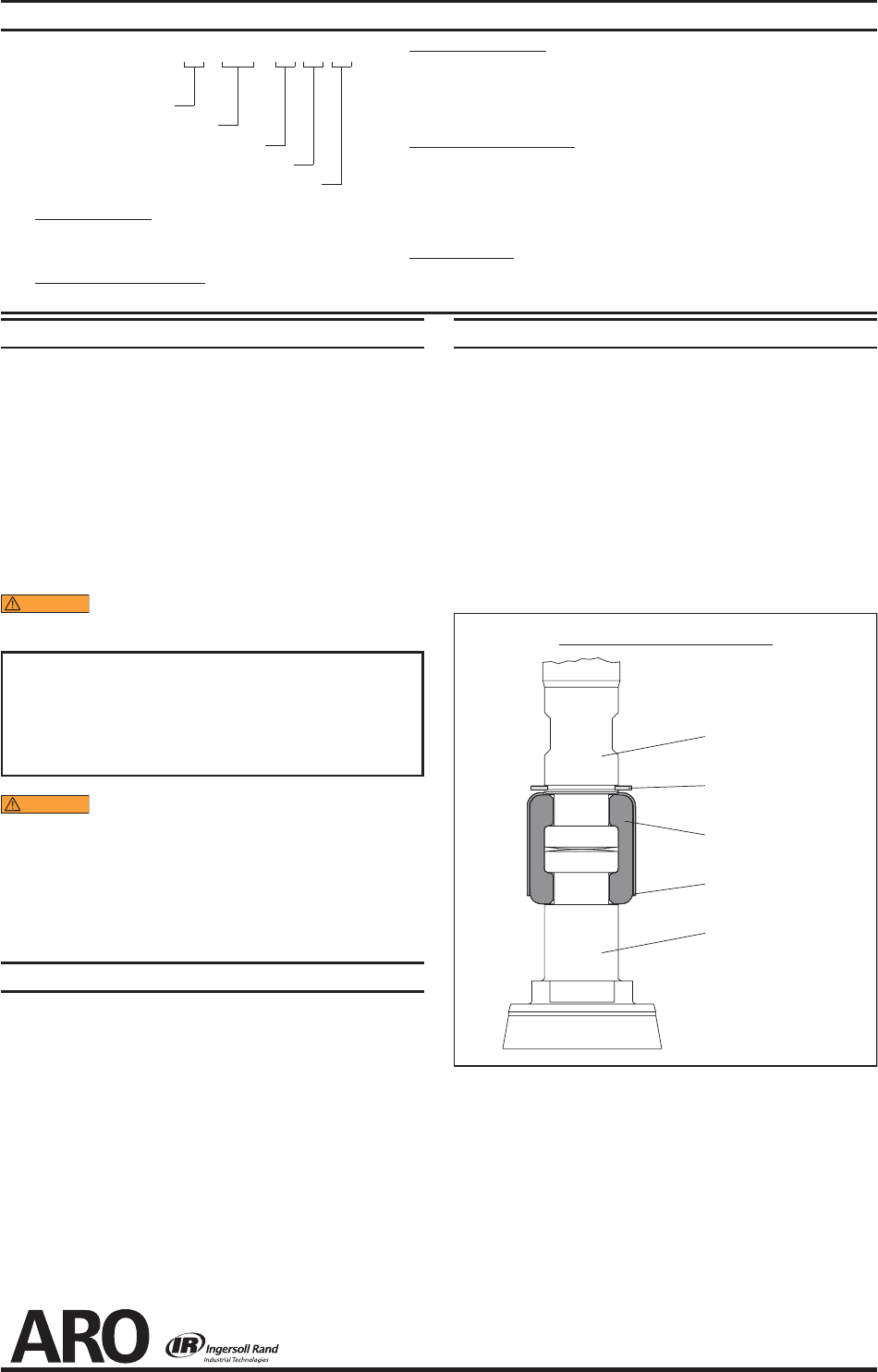
Page 2 of 2 NM2C23X-A1-XXX (en)
PN 97999-1209
GENERAL DESCRIPTION
The two-ball pumps are primarily designed for the high volume
transfer of light and medium viscosity fluids. Stainless steel con-
struction o ers compatibility with a wide range of uids. The lower
pump is designed for easy priming and the double acting feature
is standard in all ARO industrial pumps. Material is delivered to the
pump discharge outlet on both the up and down stroke.
The motor is connected to the lower pump end by a spacer section.
This allows for lubrication of the upper packing gland and prevents
motor contamination because of normal wear and eventual leak-
age through the material packing gland. Be sure the solvent cup is
adequately lled with lubricant to protect the upper packings and
insure longest service life.
WARNING
HAZARDOUS PRESSURE. Do not exceed maxi-
mum operating pressure of 2070 p.s.i. (142.8 bar) at 90 p.s.i.
(6.2 bar) inlet air pressure.
Pump Ratio X = Maximum Pump
Inlet Pressure to Pump Motor Fluid Pressure
Pump ratio is an expression of the relationship between the pump motor area
and the lower pump end area. EXAMPLE: When 150 p.s.i. (10.3 bar) inlet pressure
is supplied to the motor of a 4:1 ratio pump, it will develop a maximum of 600
p.s.i. (41.4 bar) uid pressure (at no ow) - as the uid control is opened, the ow
rate will increase as the motor cycle rate increases to keep up with the demand.
WARNING
Refer to general information sheet for additional
safety precautions and important information.
NOTICE: Thermal expansion can occur when the uid in the mate-
rial lines is exposed to elevated temperatures. Example: Material
lines located in a non-insulated roof area can warm due to sunlight.
Install a pressure relief valve in the pumping system.
Replacement warning label (pn 92325) is available upon re-
quest.
TROUBLE SHOOTING
Pump problems can occur in either the air motor section or the
lower pump end section. Use these basic guidelines to help deter-
mine which section is a ected.
Pump will not cycle.
Be certain to first check for non-pump problems including
kinked, restrictive or plugged inlet / outlet hose or dispensing
device. Depressurize the pump system and clean out any ob-
structions in the inlet / outlet material lines.
Refer to the motor manual for trouble shooting if the pump
does not cycle and / or air leaks from the air motor.
Damaged motor. Service the motor.
Pump cycles but does not deliver material.
Refer to the lower pump end manual for further trouble shooting.
y
y
y
y
PUMP CONNECTION - UPPER / LOWER
NOTE: All threads are right hand.
Lay the pump assembly on a work bench.
Remove the three (Y6-128-C) cap screws and (Y14-750-K) lock
washers from the three spacer rods (see gure 1).
Pull the air motor from the lower pump end until the motor
piston rod is in the “down” position and the lower pump end
rod is in the “up” position.
Remove the three spacer rods by removing the three (Y6-128-C)
cap screws and (Y14-750-K) lock washers.
Using e-ring pliers, slide the “e” ring up far enough to allow the
sleeve to move upward and release the two connectors (see
gure 2).
PUMP CONNECTION DETAIL
Pump Motor Piston Rod
95069 “E” Ring
Lower Pump Piston Rod
94688 Connector (2)
94689 Sleeve
Figure 2
REASSEMBLY
Align the pump motor with the lower pump end. Position the
air inlet of the motor 180° from the material outlet.
Install the two (94688) connectors and retain with the (94689)
sleeve. Slide the (95069) “e” ring back into position.
Assemble the three (93866) spacer rods to the lower pump and
secure using three (Y14-750-K) lock washers and (Y6-128-C)
cap screws.
Reinstall the spacer rods to the pump motor.
Bring the motor and lower pump together and retain with
three (Y14-750-K) lock washers and (Y6-128-C) cap screws.
1.
2.
3.
4.
5.
1.
2.
3.
4.
5
.
PUMP OPTION DESCRIPTION CHART
NM2C23 X - A1 - X X X
Packing Material
Spring Arrangement
Plunger Type
PACKING MATERIAL
(Packings are upper and lower unless noted)
C - UHMW-PE P - UHMW-PE / PTFE staggered (upper)
K - Carbon Graphite lled PTFE UHMW-PE (lower)
L - Mineral lled PTFE R - PTFE / UHMW-PE staggered (upper)
Mineral lled PTFE (lower)
SPRING ARRANGEMENT
3 - No spring E - Wave spring with alternate solvent cup
6 - Wave spring F - No spring with alternate seat material
8 - No spring with alternate solvent cup and alternate solvent cup
C - No spring with alternate seat material G - Wave spring with alternate seat material
D - Wave spring with alternate seat material and alternate solvent cup
PLUNGER TYPE
D - Hard stainless steel with hard chrome plating
F - Stainless steel with hard chrome plating
y
ARO® is a registered trademark of Ingersoll-Rand Company
y
Pump Material
Container Suitability
PUMP MATERIAL
G - 400 series stainless steel
H - 300 series stainless steel
CONTAINER SUITABILITY
A1 - Universal (stub)