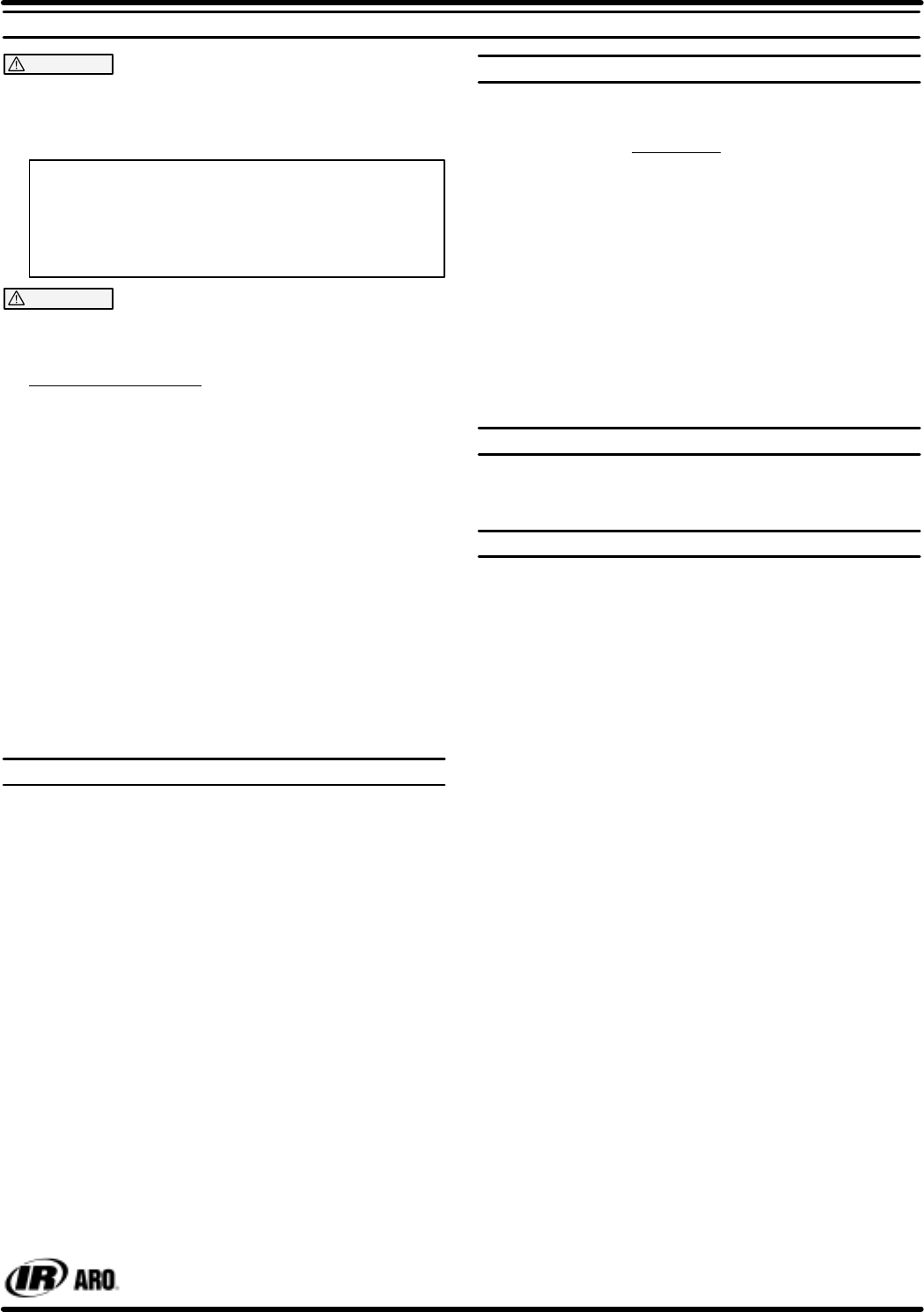
LP3001Ć1
PAGE2OF2
PLACING INT
O SER
VICE
WARNING EXCESSIVE INLET PRESSURE. Can cause exĆ
plosion resultinginsevereinjuryor death.Do notexceedmaxĆ
imum operating pressure of 7500 p.s.i. (517 bar) at 150 p.s.i.
(10.3 bar) inlet air pressure. Do not run pump without using a
regulator to limit air supply pressure to the pump.
PUMP RATIO X
INLETPRESSURETOPUMP MOTOR
=
MAXIMUMPUMP
FLUIDPRESSURE
Pumpratioisanexpression oftherelationshipbetweenthepumpmotorareaand
thelowerpumpend area.EXAMPLE:When 150p.s.i. (10.3bar)inlet pressureis
suppliedtothemotorofa 50:1ratiopumpitwilldevelopamaximumof7500p.s.i.
(517bar)fluidpressure(atnoflow)Ćasthefluidcontrolisopened,theflowratewill
increase as the motor cycle rate increasesto keep up with the demand.
WARNING EXCESSIVE MATERIAL PRESSURE. Can cause
equipment failure resulting in severe injury or property damĆ
age. Do not exceed the maximum material pressure handling
capability of any component in the system.
Thermal expansionhazard.This canoccurwhen thefluidinthemaĆ
terial line is exposed to elevated temperatures. Example: Material
line located in a nonĆinsulated roof area can warm due to sunlight.
Install apressure reliefvalve inthepumping systemifthis condition
could exist.
AIR AND LUBRICATION REQUIREMENTS
Filtered air will help extend the life of the pump, allowing the pump to
operate moreefficientlyand yieldlonger servicelifeto movingpartsand
mechanisms.
• Use an air linefilter to provide good qualityclean and dry air, install
it up stream from the air regulator.
• Use anairregulator onthe airsupply tocontrolthe pumpcycle rate,
install the regulator as close as possible to the pump.
• In mostinstallations lubricationis notrequired. Ifthepumpneedsto
have lubrication, install an air linelubricator between thepumpand
the airregulatorand supplyit withagood gradeof nonĆdetergentoil
or other lubricant compatible with Nitrile seals. Set at a rate not to
exceed one drop per minute.
INSTALLATION
Assemble components included in the package as shown in figure 1.
NOTE: In rigid plumbing applications,use flexible material and air supĆ
ply hoses when attaching the pump to prevent damage by vibration.
1. Thread the pump bung adapter into the pump cover, insert the
pump into the bung and then secure with the thumb screws proĆ
vided.
2. Install the handle and secure with the four nuts provided with the
cover.
3. Install the outlet adapter, material hose, swivel and gun.
4. Lay the follower on top of a full bucket of grease, feed the lower
pump end into the follower and secure the cover with the thumb
screws.
5. Attach the coupler to the air supply hose and the connector to the
pump air inlet adapter.
6. Connect the material hose to the pump outlet. Tighten all fittings.
Use caution not to damage threads.
OPERATION
STARTĆUP
1. Turn the air regulator to 0" pressure setting. Connect the air hose.
2. Prime the pump by cycling slowly, raising the pressure to 20 Ć 30
p.s.i. Cycle the pump until the test grease and any trapped air has
been purged from the system.
3. Close the dispensing device. Allow the pump tobuild line pressure
and stall. Check for any leaks and reĆtorque fittings if needed. AdĆ
just air pressure upward as required for the application.
NOTICE: Ifthe pumpdoesnot primesoonafter initialstartĆup,establish
whattheproblem isto preventunnecessary damageto thepump plungĆ
er.
SHUTDOWN
• Disconnect the air supply from the pump if it is to be inactive for a
few hours. Open the dispensing device to relieve line pressure.
SERVICE
Refer to thebasic pumpmanual forservice instructionswhich alsocovĆ
ers disassembly and reassembly for installation of the rebuild kit.
TROUBLE SHOOTING
If the pump does not cycle or will not deliver material.
• Be certain to check for nonĆpump problems including kinked, reĆ
strictive or pluggedinlet /outlet hoseordispensing device.DepresĆ
surize thepump systemand cleanout anyobstructions inthe inlet /
outlet material lines.
• Check all seals, including track gaskets.
PN97999Ć702