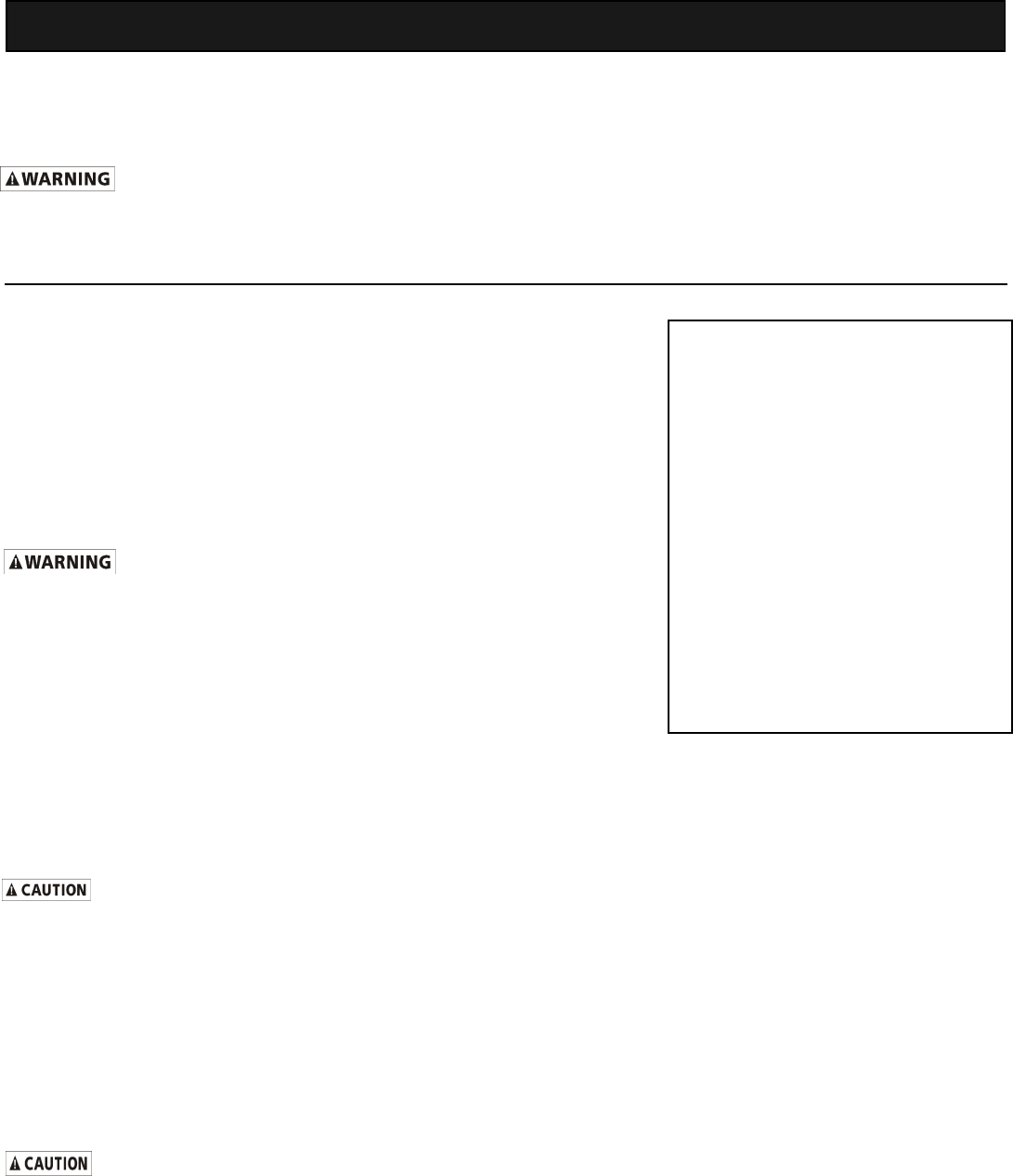
Please read and save this Repair Parts Manual. Read this manual and the General Operating Instructions carefully before attempting to assemble, install,
operate or maintain the product described. Protect yourself and others by observing all safety information. The Safety Instructions are contained in the General
Operating Instructions. Failure to comply with the safety instructions accompanying this product could result in personal injury and/or property damage! Retain
instructions for future reference. AMT reserves the right to discontinue any model or change specifications at any time without incurring any obligation.
©2006 American Machine & Tool Co., Inc. of PA, A Subsidiary of The Gorman-Rupp Company, All Rights Reserved.
Periodic maintenance and inspection is required on all pumps to insure proper operation. Unit must be clear of debris and sediment. Inspect for leaks and loose
bolts. Failure to do so voids warranty.
3 Inch Self-Priming Centrifugal Pumps
Refer to form 1808-634-00 for General Operating and Safety Instructions.
Description
These centrifugal pumps are self-priming (to 20 ft. lift) units designed for high volume
liquid transfer – irrigation, de-watering, lawn sprinkling, etc. They can also accommodate
semi-solids (up to 1/2" dia.), sediment laden liquids, and liquids with entrained air or
gases. Casing working pressure to 100 psi (689 kPa).
The units are equipped with a cast iron pump casing designed with a full dual volute, clog
resistant semi-open stainless steel/bronze impeller, and a cast iron adapter. Units are
equipped with flapper valves to assure a positive prime. A mechanical seal isolates the
motor from the liquid in the pump casing. The units are coupled to 3600 RPM, totally
enclosed fan cooled motors. All units are manual models, no controls are supplied. For
use with nonflammable, non-abrasive liquids compatible with pump component materials.
Maintenance
Make certain that unit is disconnected from power source before
attempting to service or remove any component.
NOTE: Pump casing should be removed and inspected periodically to insure that any
foreign material or rust is not clogging internal pump parts. This unit is equipped with a
dual volute pump casing. One of the volutes runs 180°, all the way from side opposite
discharge into discharge through a completely enclosed passageway. If foreign material
clogs this area, it can be dislodged by using a wire or long spring.
REMOVAL OF OLD SEAL
Refer to Figure 1
IMPORTANT: Always replace both seal seat (Ref. No. 10) and seal head (Ref. No. 11)
to insure proper mating of components! Also, impeller seal washer (Ref. No. 14) should
be replaced anytime impeller lock bolt (Ref. No. 15) has been removed.
1. Remove four bolts (Ref. No. 4) that connect adapter (Ref. No. 7) to casing (Ref.
No. 16).
2. Remove casing and casing seal (Ref. No. 8).
Care should be taken not to "pinch" or "shave" the o-ring gasket
(Ref. No. 8) between adapter and casing.
3. Using an Allen wrench, remove impeller lock bolt, impeller seal washer, and
impeller (Ref. No. 13).
IMPORTANT: Care should be taken to insure that same number of shim washers
(Ref. No. 12) are replaced behind impeller as were removed. These shim washers are
located directly behind impeller. These washers as well as impeller key (Ref. No. 2)
become loose as impeller is removed.
4. Seal head and shaft sleeve can now be pulled from shaft.
5. Pry seal seat from adapter.
6. Push seal head from shaft sleeve.
INSTALLATION OF NEW SEAL
The precision lapped faces on mechanical seal are easily damaged.
Handle your replacement seal carefully.
1. Thoroughly clean all surfaces of seal seat cavity.
2. Using a clean cloth, wipe shaft and shaft sleeve and make certain that they are
perfectly clean.
3. Wet the rubber portion of new seal seat with a light coating of soapy water. While
wearing clean gloves or using a clean light rag, press seal seat squarely into adapter
recess. Avoid scratching polished surface. If seal will not position properly, place a
cardboard washer over polished surface and use a piece of pipe to press in, firmly but
gently.
Specifications
Suction inlet ...................3" NPT
Discharge outlet ................3" NPT
Motor (TEFC) . . . 3 HP(Model 2874 & 2877)
.............. 5 HP (Model 2875 & 2878)
...................7.5 HP (Model 2876)
Power Supply:
Model 2874, 2875, 2876:
........... 230/460 VAC, 60 Hz, 3 Phase
Models 2877 and 2878:
............... 230 VAC, 60 Hz, 1 Phase
RPM .......................... 3600
Pump construction ............ Cast Iron
Impeller material......... Stainless Steel
STD Mechanical Seal .....Carbon/ceramic
...........Buna-N, S.S. springs and parts
Liquid temp.... 40° to 180° F (4° to 82° C)
NOTE: Data is subject to change without
notice.
4. Dispose of cardboard washer. Check
again to see that polished surface is free
of dirt and all other foreign particles and
that it has not been scratched or
damaged.
5. Wet the inside of rubber portion of new
seal head with a light coating of soapy
water. Slide head onto shaft sleeve. Slide
shaft sleeve with seal head onto motor
shaft. Seal head and seal seat will meet.
Reinstall any shims which have been
removed. (See SHIM ADJUSTMENT
section.)
6. Replace impeller key and impeller.
Replace impeller seal washer before
screwing impeller lock bolt in place.
7. Reassemble pump.
8. A short "run-in" period may be necessary
to provide completely leak free seal
operation.
SHIM ADJUSTMENT
When installing a replacement impeller (Ref.
No. 13) or motor (Ref. No. 1), it may be
necessary to adjust the number of shims
(Ref. No. 12) to insure proper running
clearance between impeller and casing (Ref.
No. 16). Proceed as follows:
NOTE: A proper running clearance is less
than 0.010".
1. For impeller replacement, add one (1)
Specifications Information and Repair Parts Manual 2874-95 thru 2878-95
2874-251-00 05/2007