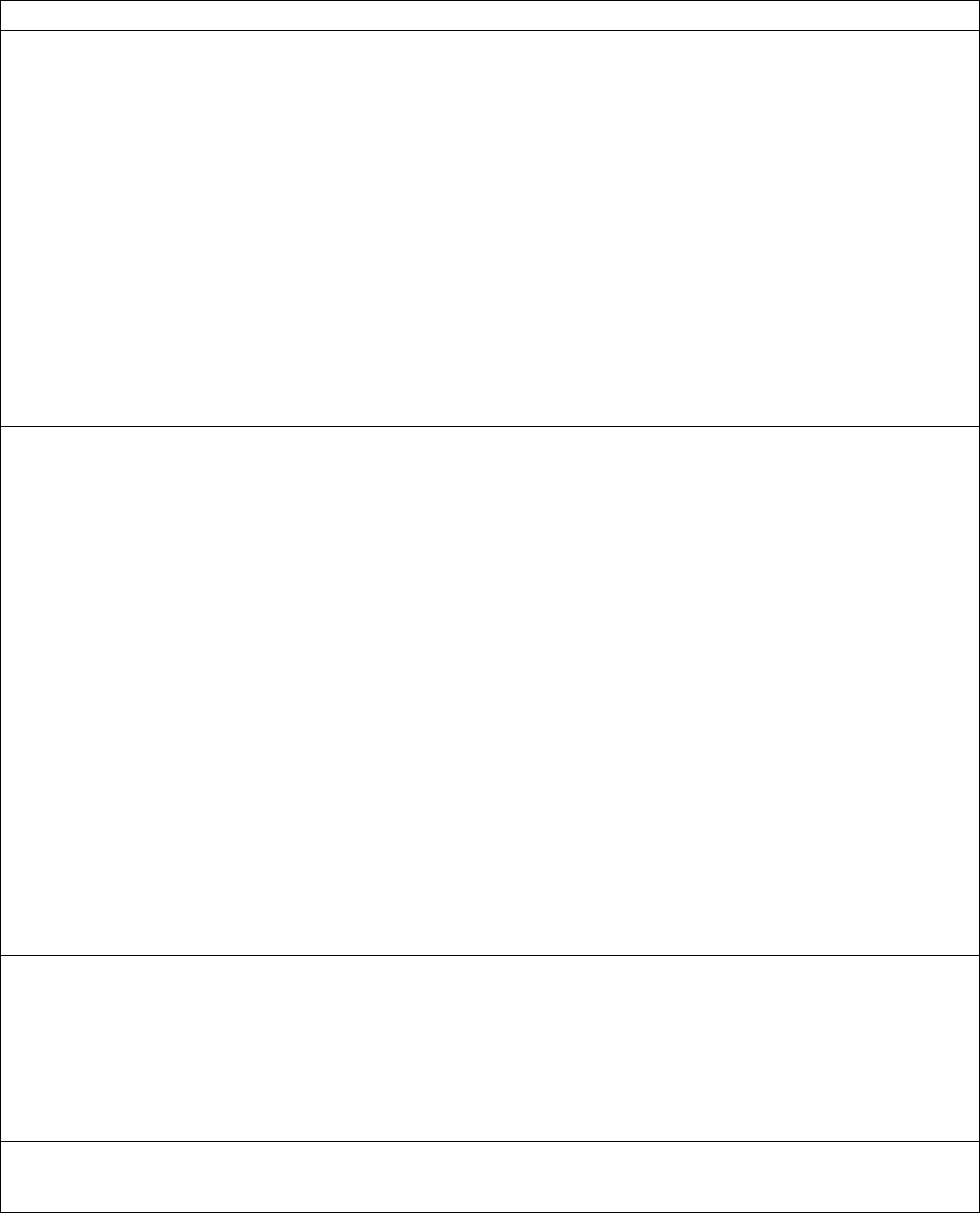
11
FLINT & WALLING, INC. • 95 North Oak St. • Kendallville, IN 46755 • www.flintandwalling.com
Troubleshooting Chart
Symptom Possible Cause(s) Corrective Action
Pump won’t
start or run
at full speed
1. Blown fuse or open circuit breaker 1. Replace fuse or close circuit breaker. See wire size chart for
proper break/fuse size
2. Power supply in OFF position 2. Turn power on
3. Incorrect voltage at motor (check volt-
age with motor running)
3. Low voltage
a. Voltage must be within ± 10% of motor rated voltage.
Check incoming voltage. Contact power company
b. Make certain that voltage of motor matches voltage of
power supply. See motor name plate and motor wiring
diagrams
c. Check wire size from main switch to pump. See wire
size chart for correct wire size
4. Loose, broken or incorrect wiring 4. Rewire any incorrect circuits. Tighten connections, replace
defective wires
5. Defective motor 5. Replace motor
6. Pump hydraulic components clogged/
worn/damaged
6. Replace worn parts or entire pump. Clean parts if required
Pump oper-
ates, but
delivers little
or no water
1. Manual or solenoid valves plumbed
into system restricting flow
1. a Check all valves on pump inlet and discharge sides of
system to be sure they are opened properly to allow
flow to and from the pump
b. Bleed trapped air in pump which keeps water from
reaching the pump. (Normally
due to closed valve in discharge plumbing)
2. In-line filter restricting flow 2. Check all in-line filters to be sure they are not plugged or
restricted
3. Low line voltage 3. See low line voltage corrective action (above)
4. Inadequate water supply to booster
pump
4. Check pressure on inlet side of booster to be sure positive
pressure is maintained to the booster pump
5. Undersized piping 5. Replace undersized piping
6. Leak on inlet side of system 6. Make sure connections are tight. Repair leaks as necessary
7. Inadequate, defective or plugged foot
valve and/or strainer
7. Clean, repair or replace as needed
8. Worn or defective pump parts or
pump.
8. Replace worn parts or entire plugged impeller Clean parts if
9. Suction lift too great 9. Pump should be operated under
flooded suction only
10. Pump not primed 10. Prime pump - Make certain inlet pipe is drawn up tight and
pump and pipe are full of water
11. Incorrect rotation, motor running
backwards
11. Reverse motor rotation can occur on three phase units. To
correct, interchange any two incoming power leads.
Excessive
noise while
pump in
1. Pump not secured to firm foundation 1. Secure properly
2. Piping not supported 2. Make necessary adjustments
3. Restricted inlet line 3. Clean or correct
4. Cavitation (noise like marbles in pump) 4. a. Reduce speed on direct drive
b. Increase inlet pipe size
c. Too viscous (material being pumped too thick
5. Worn motor bearings 5. Replace bearings or motor
Pump leaks 1. Worn mechanical seal (leaks at shaft) 1. Replace shaft (rotary) seal
2. Worn o-ring seals 2. Replace o-ring seals, located inside both ends of the stainless
steel shell