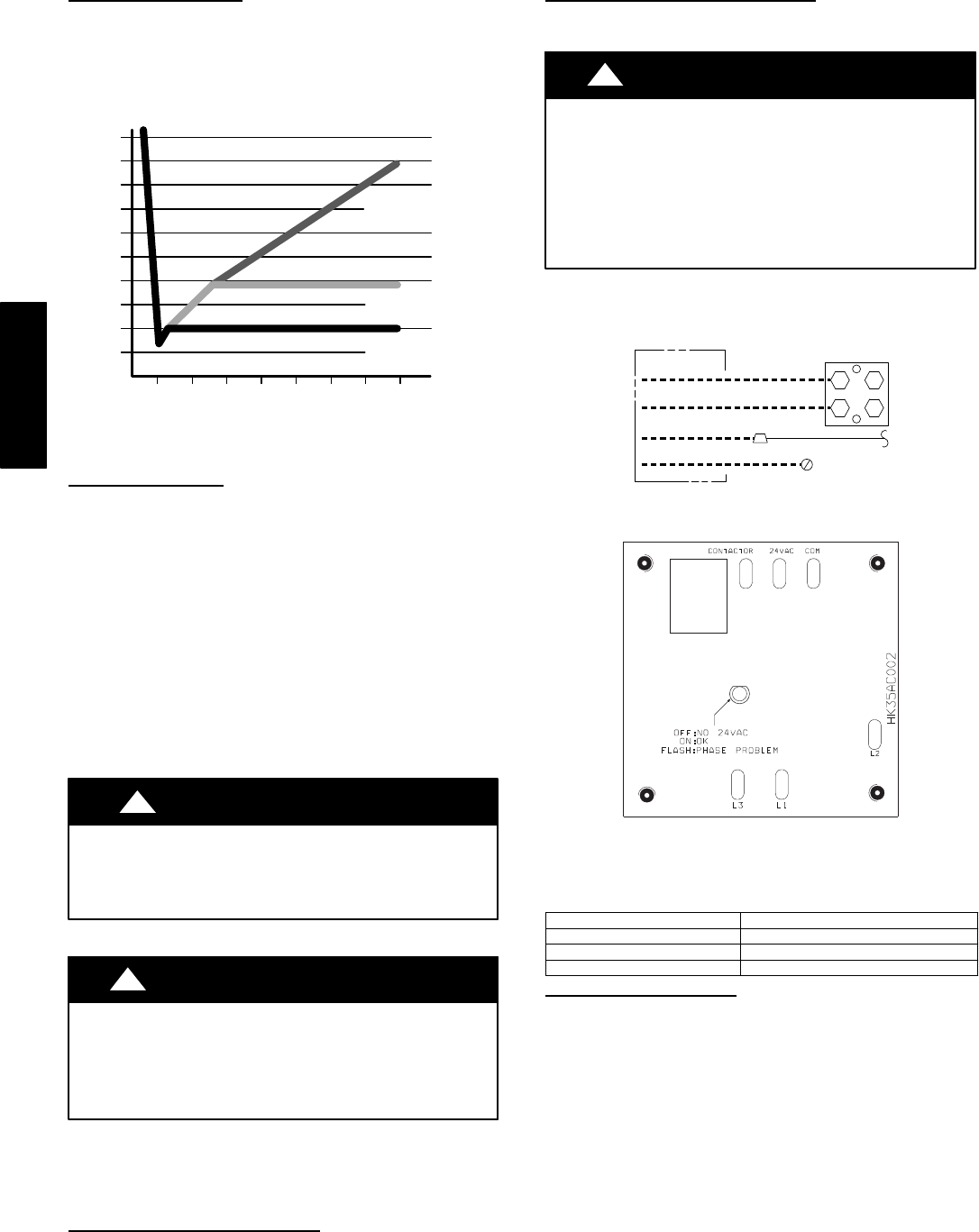
4
Deep Vacuum Method
The deep vacuum method requires a vacuum pump capable of
pulling a vacuum of 500 microns and a vacuum gage capable of
accurately measuring this vacuum depth. The deep vacuum method
is the most positive way of assuring a system is free of air and
liquid water. A tight dry system will hold a vacuum of 1000
microns after approximately 7 minutes. See Fig. 6.
500
MINUTES
01234567
1000
1500
LEAK IN
SYSTEM
VACUUM TIGHT
TOO WET
TIGHT
DRY SYSTEM
2000
MICRONS
2500
3000
3500
4000
4500
5000
A95424
A95424
Fig. 6 -- Deep Vacuum Graph
Final Tubing Check
IMPORTANT: Check to be certain factory tubing on both indoor
and outdoor unit has not shifted during shipment. Ensure tubes are
not rubbing against each other or any sheet metal. Pay close
attention to feeder tubes, makings sure wire ties on feeder tubes are
secure and tight.
Be sure field wiring complies with local and national f ire, safety,
and electrical codes, and voltage to system is within limits shown
on unit rating plate. Contact local power company for correction of
improper voltage. See unit rating plate for recommended circuit
protection device.
NOTE: Operation of unit on improper line voltage constitutes
abuse and could a ffect unit reliability . See unit rating plate. Do not
install unit in system where voltage may fluctuate above or below
permissible limits.
CAUTION
!
UNIT DAMAGE HAZARD
Failure to follow this caution may result in equipment damage
or improper operation.
Installation of filter drier in liquid line is required.
Make Electrical Connections
!
WARNING
ELECTRICAL SHOCK HAZARD
Failure to follow this warning could result in personal injury or
death.
Do not supply power to unit with compressor terminal box
cover removed.
NOTE: Use copper wire only between disconnect switch and unit.
NOTE: Install branch circuit disconnect of adequate size per NEC
to handle unit starting current. Locate disconnect within sight from
and readily accessible from unit, per Section 440--14 of NEC.
Route Ground and Power Wires
Remove access panel to gain access to unit wiring. Extend wires
from disconnect through power wiring hole provided and into unit
control box.
Connect Ground and Power Wires
Connect ground wire to ground connection in control box for
safety. Connect power wiring to contactor as shown in Fig. 7.
!
WARNING
ELECTRICAL SHOCK HAZARD
Failure to follow this warning could result in personal injury or
death.
The unit cabinet must have an uninterrupted or unbroken
ground to minimize personal injury if an electrical fault should
occur. The ground may consist of electrical wire or metal
conduit when installed in accordance with existing electrical
codes.
Connect ground wire to ground connection in control box for
safety. Connect power wiring to contactor as shown in Fig. 7.
DISCONNECT
PER N.E.C. AND/OR
LOCAL CODES
CONTACTOR
GROUND
LUG
FIELD GROUND
WIRING
FIELD POWER
WIRING
BLUE
3 PHASE ONLY
A94025
Fig. 7 -- Line Connections
A00010
Fig. 8 -- 3--Phase Monitor Control
(Applies t o 3--Phase Units Only)
Table 3 – 3-- Phase Monitor LED Indicators
LED STATUS
OFF Nocallforcompressoroperation
FLASHING Reversed phase
ON Normal
Connect Control Wiring
Route 24v control wires through control wiring grommet and
connect leads to control wiring. See Thermostat Installation
Instructions for wiring specific unit combinations. (See Fig. 9.)
Use No. 18 AWG color--coded, insulated (35°C minimum) wire. If
thermostat is located more than 100 ft (30.5 m) from unit, as
measured along the control voltage wires, use No. 16 AWG
color--coded wire to avoid excessive voltage drop.
All wiring must be NEC Class 1 and must be separated from
incoming power leads.
Use furnace transformer , fan coil transformer, or accessory
transformer for control power, 24v/40va minimum.
NOTE: Use of available 24v accessories may exceed the
minimum 40va power requirement. Determine total transformer
223A / 224A