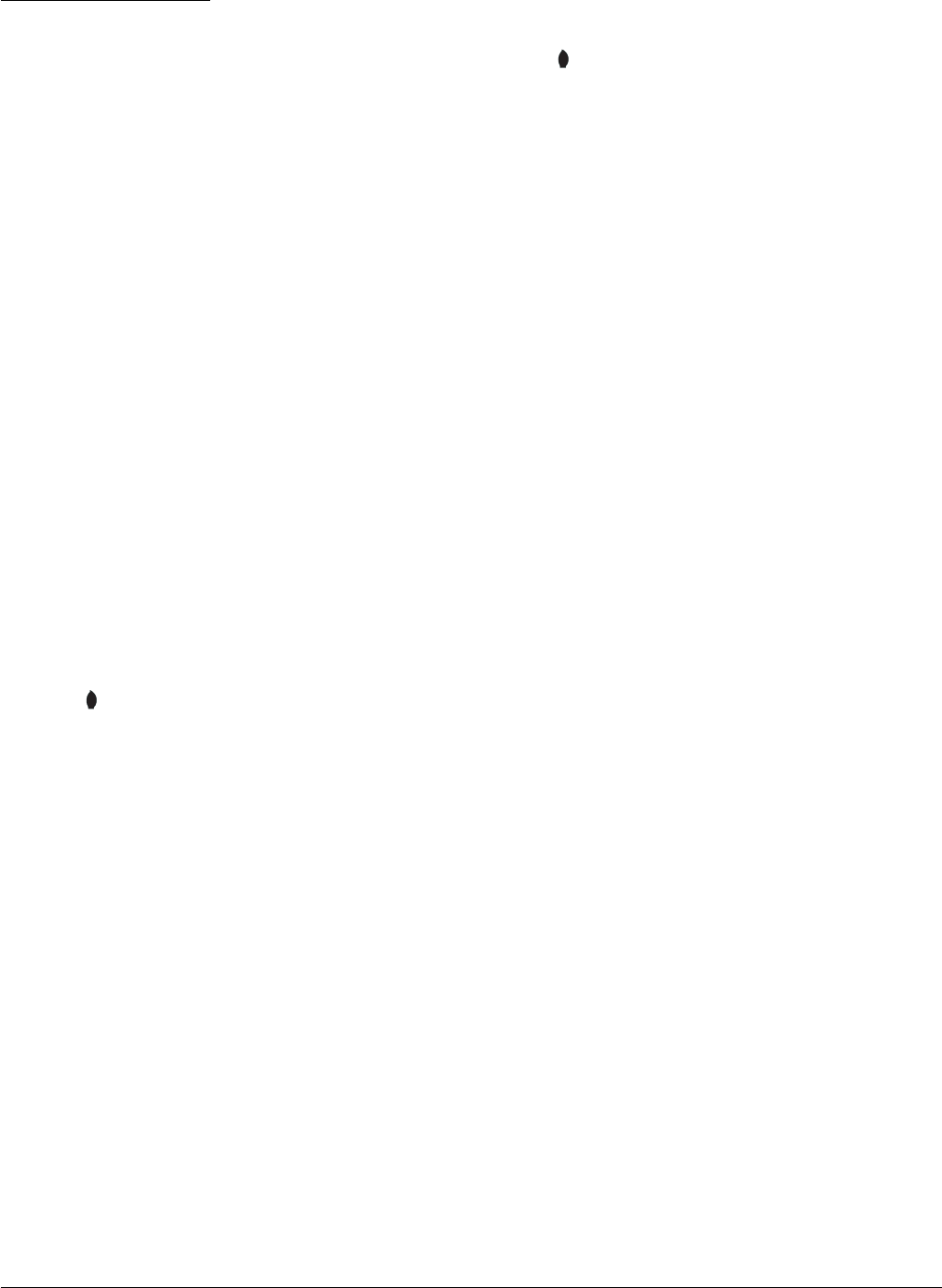
14 6 720 606 518
If some burners have yellow flames while others have good
flames, it is likely that dust, lint or spider webs have partially
clogged the burner venturis. Contact a gas service person
to clean the remove and clean the burners.
Mineral Scale Build-up: The AquaStars heater, when
operated at lower temperatures settings, do not accumulate
mineral build-up. If however, the water has a high mineral
content, periodic descaling may be necessary. The heating
coils should be flushed with a descaling solution. Consult
your service person.
TROUBLE SHOOTING (see maintenance table)
Introduction
The AquaStar 125 B “S” burners are activated by a water
flow valve. Numerous water related problems can cause
this water valve to malfunction such as: Insufficient water
flow volume to activate the burners at its minimum flow
requirement; Dirt in the water flow valve causing it to
malfunction; Sediment build-up in faucet aerators, or shower
heads; Uneven pressures between cold and hot. (with single
lever faucets) Plumbing cross overs. These water flow related
problems can cause the heater to deliver less than its full
output, or to fail to ignite or to shut down completely.
Problems are stated in upper case, bold face. Most common
causes for the problems follow in order of likelihood. The
suggested solutions require that the cover be taken off. To
do this, remove incandescent particle tray and unscrew the
central screw located at the bottom of the front cover. Pull
main cover out toward you and lift up and out.
PILOT LIGHT WILL NOT LIGHT
1. No gas to the AquaStar
A. Gas cock on gas line may not be open.
B. Gas valve button has not been pushed in on “PILOT”
position ( ).
C. Gas regulator may be shut or damaged.
2. In-line AquaStar gas regulator jammed (usually on
LP gas)
Replace or unlock the regulator. Note: The regulator
furnished with the heater is designed for low gas pressure.
Excessive pressure will lock it up (propane only). Locking
usually happens if the gas pressure between the gas tank
(propane) and the water heater’s gas regulator has not been
reduced. See page 2 for recommended correct gas pressure.
To unlock a regulator, consult your gas supplier.
3. Pilot orifice clogged and/or air screen dirty, or pilot
gas filter is dirty.
Clogging of the pilot burner can be caused by dust and any
suspended matter contained in the ambient air.
Although the filters can lengthen the cleaning intervals, they
can never completely prevent such clogging. In consequence
the gas jet issuing from the pilot orifice is reduced and or
the air mixture is reduced. The pilot flame is weak and thus
can no longer heat the thermocouple sufficiently. For cleaning
purposes, the air filter screen is pulled off, washed and blown
out. The pilot orifice has likewise to be cleaned or exchanged.
Consult a gas service person to clean the pilot.
4. Air in the Gas Line
Note: Normally this is a problem only at the time of initial
installation, after the pipes have been worked on, or after a
propane tank has been allowed to empty, or after the heater
has been shut down for a long time.
Bleed all the air trapped in the gas line. Because of the very
small pilot orifice (especially on LP gas models), bleeding
out all the air could take several minutes. Depress the pilot
button ( ) and depress this button until all the air has
escaped, and the gas has arrived. During this process, press
repeatedely on the piezo ignition button until the pilot flame
has ignited.
PILOT LIGHTS BUT FLAME GOES OUT WHEN BUTTON
IS RELEASED
1. Pilot push button was not pushed in far enough or
was not held in long enough
Depress the pilot button. Hold it pushed in for at least 15
seconds to give time for the pilot flame to properly heat the
tip of the thermocouple.
2. Pilot flame improperly aimed or is too weak so it is
not properly heating the tip of the thermocouple.
The Pilot flame should be a sharp blue flame and aimed at
the tip of the thermocouple so that it envelops 10 mm (3/8
“) of the thermocouple tip. Pilot flame has to be properly
aimed at the thermocouple. See Fig 8.
3. Poor thermocouple connection at the electromagnet
Note: Electromagnet is part #8707201094 located on the
right side of the gas valve behind the piezo pushbutton
assembly. Check the tightness of the thermocouple
connection nut at the electromagnet: The Electro-magnet
connection is a large aluminum 17mm hex head nut. The
thermocouple end is a 5 mm brass nut which screws into
the 17 mm nut. Tighten the thermocouple nut snugly but not
too tight.
4. Poor circuit connections at the ECO. (Energy Cut-
Off overheat protection)
Oxidation or looseness of the ECO terminal connections
can result in millivolt current loss through the thermocouple
safety circuit. Clean terminals with very fine sand paper or
an eraser and reconnect ECO leads.
5. Faulty ECO (part #8707206017)
If cleaning the terminals attached to the ECO did not fix the
problem, connect a jumper wire between the two wires and
try to relight the pilot. If the pilot flame now remains on,
replace the ECO. If the flame still goes out when the button
is released, the ECO is not defective. Go to next step.
6. Faulty thermocouple (part #8747202083) or
electromagnet) Unless these 2 parts are at least 8 to
10 years old, it is very unlikely that they are faulty.
Before testing, reconfirm that #2 is absolutely correct,
and that all connections are clean and tight.