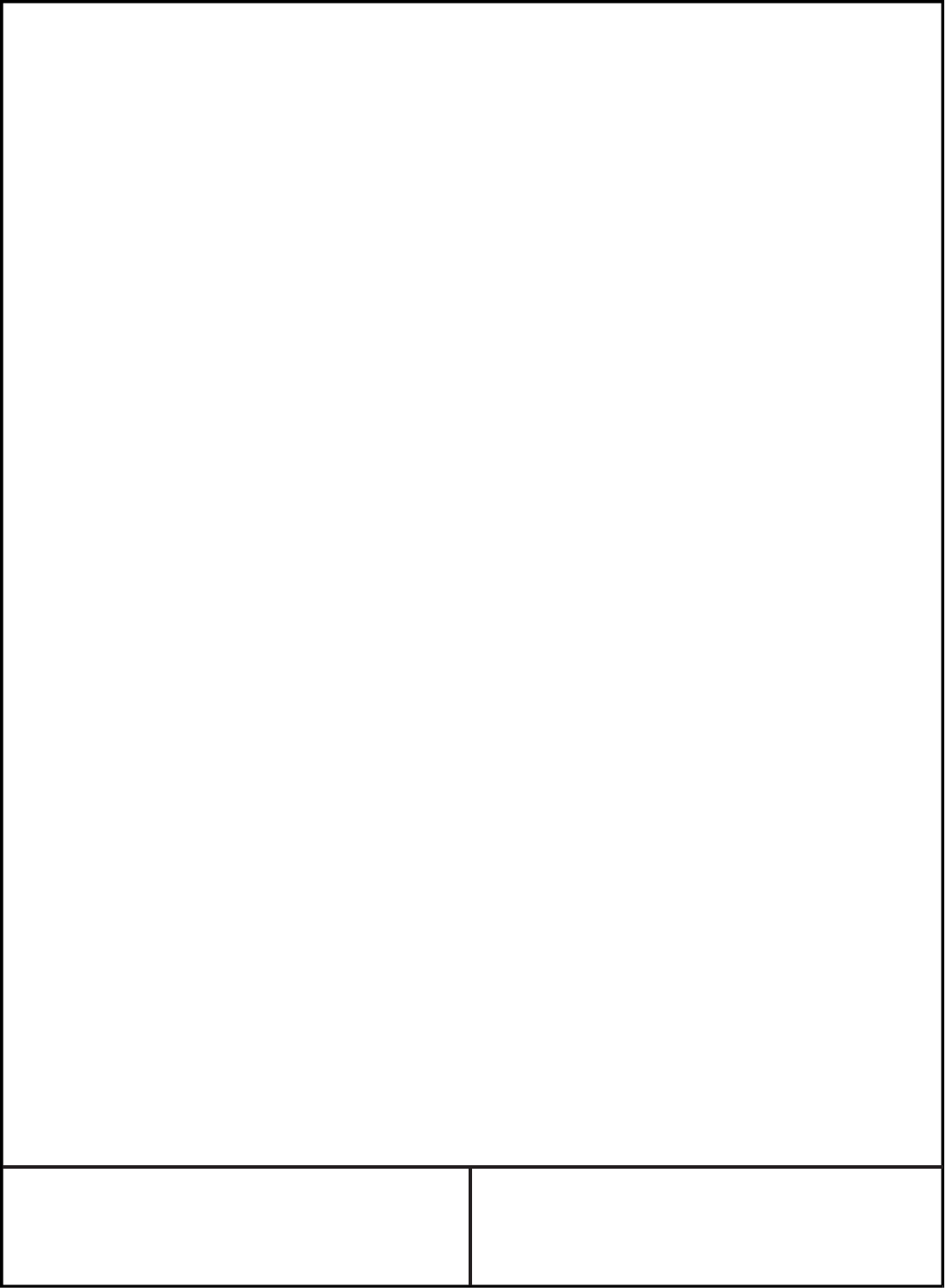
A. O. Smith
Water Products Company
Ashland City, TN
A Division of A. O. Smith Corporation
A. O. Smith Corporation reserves the right to make product changes
or improvements at any time without notice.
Printed in U.S.A.
A 012.18
© A. O. Smith Corp., 2003
A.O. Smith Water Products Co., Inc. On Line
www.hotwater.com
For Technical Information and
Automated Fax Service,
Phone: 800-527-1953
SUGGESTED SPECIFICATIONS
The hot water supply boiler(s) shall be an A.O. Smith Genesis Model GW _________ having an input rating of ________ BTU/hr,
and an output rating of ________ Btu/hr when fired with (Natural/Propane) _________ gas. The boiler shall bear the ASME “H”
stamp and shall be National Board registered (CRN in Canada) for 160 PSI working pressure. The boiler(s) shall be equipped
with a factory installed 125 PSIG ASME Pressure Relief Valve.
The boiler(s) shall be design tested and certified to the ANSI Z21.13 standard and approved by the American and Canadian Gas
Associations with a listed thermal efficiency of 84%.
The boiler’s copper fin tube heat exchanger shall be a horizontal, double row, two pass, 15-tube design. The lower first pass with
8 solid copper tubes, shall have integral extruded copper fins spaced at “5” fins per inch, the upper second pass with 7 solid
copper tubes shall have “7” extruded copper fins per inch. The tubes shall be rolled into heavy (all Bronze “Standard” /or Cast Iron
CoraShield lined ”optional”) ___________________headers. The ASME approved bolted split headers must have a removable
faceplate that allows full access and inspection of the tubes and internal header surfaces. Non-removable one-piece headers,
with small inspection plugs, shall not be acceptable.
The heat exchanger shall bear a 5-year manufacturer’s limited warranty against failure. The heat exchanger shall be immune to
thermal shock.
The Boiler(s) shall be provided with the factory sized, integrally rear header mounted, pre-wired, bronze fitted, factory installed
pump. The pump shall be controlled by the boiler’s Dia-Scan II control and include an adjustable time delay, that allows the
removal of useable residual heat from the combustion chamber and cools the boiler to an equal system temperature during the
stand-by cycle.
The combustion chamber shall be fully lined with lightweight, high temperature ceramic fiber insulation, rated to 2,300°F (1260°C).
The jacket panels shall be powder coated with a baked-on finish, which is suitable for outdoor service. The jacket shall be of tight
construction, and weather and water-resistant.
The boiler shall employ a fan induced premixed multi-burner system firing into a pressurized combustion chamber. The “4509”
stainless steel/titanium alloy burners shall be fired using Pre-Jet gas orifices that provide precise gas to air mixture for clean
combustion and low NOx operation. The pre-Jet gas orifices shall be self-adjusting for altitude, from sea level to 6,000 feet
(1,830m). The boiler(s) shall be capable of meeting or exceeding the current national, state, and local air quality regulations for low
NOx.
All electrical boiler functions shall be controlled, operated, and monitored by a Dia-Scan II microprocessor-based control. The Dia-
Scan II control shall provide (three “GW-1000 thru GW-1500”/four “GW-1850 thru GW-2500) _____ stage operation. Each stage
shall be adjustable by the operator to allow the boiler to be adjusted to suit the application and maximize system/boiler efficiency
and operation. The microprocessor shall control the boiler temperature and be accurate to within plus or minus 1°F. The hot
surface ignition system shall employ a separate flame sensor for each stage to provide maximum safety. The microprocessor-
based boiler control shall be tested to ANSI standards and approved by both UL and AGA/CSA.
The boiler shall be supplied with a remote tank thermistor for sensing and controlling the storage tank temperature up to 1,000 feet
(300m) away by the Dia-Scan II boiler control. Alternate 24V contacts shall also be provided to allow the boiler to be controlled by
energy management systems and/or multi-boiler controllers.
The microprocessor-based control shall be self-diagnostic and provide 25 LED’s that indicate current operating and fault status.
In addition to the LED’s, a digital LED enunciator shall provide numerical read outs of inlet/outlet, inlet/outlet differential, set point
and set point differential temperatures; along with additional numerical failure codes.
Factory mounted and wired flow, blower prover, and blocked flue switches shall be provided. The gas train shall meet or exceed the
requirements of ANSI Z21. 13 and include gas pressure regulator, manual gas cock, redundant safety gas valve, operating control
valve, and plugged pressure test tapings.
The boiler(s) shall be AGA/CSA approved for direct horizontal through the wall venting, or direct vertical venting; in addition to
conventional sidewall or conventional vertical venting. The boiler(s) must be field convertible from top mounted venting to rear
mounted venting.
For maximum floor space optimization, the boiler(s) will have the option of being stacked directly one above the other using a
factory designed Stack-Rack as provided by the manufacturer. Boilers with top only vent outlets that cannot be stacked directly one
above the other are not acceptable.