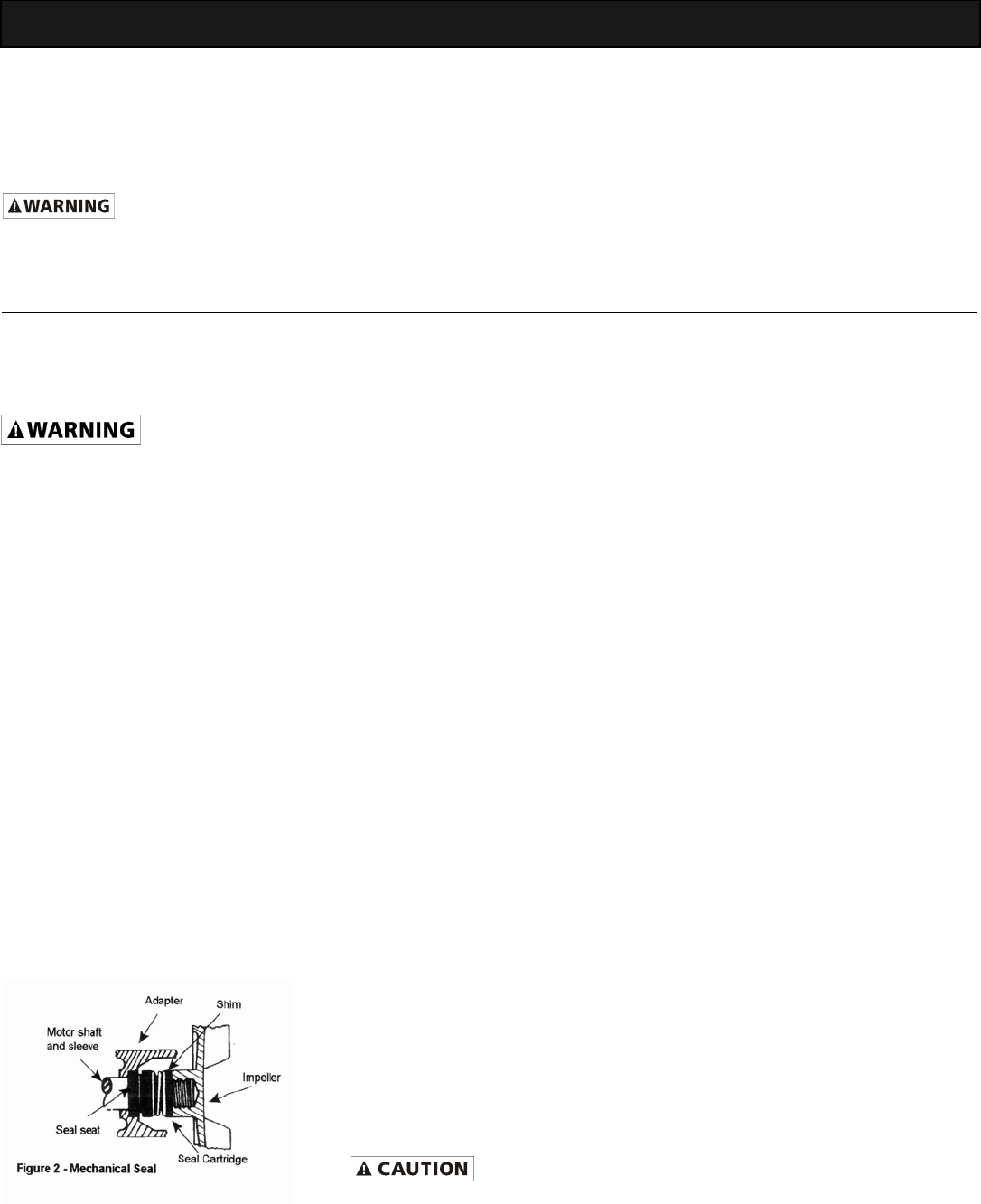
Please read and save this Repair Parts Manual. Read this manual and the General Operating Instructions carefully before attempting to assemble,
install, operate or maintain the product described. Protect yourself and others by observing all safety information. The Safety Instructions are contained
in the General Operating Instructions. Failure to comply with the safety instructions accompanying this product could result in personal injury and/or
property damage! Retain instructions for future reference. AMT reserves the right to discontinue any model or change specifications at any time without
incurring any obligation.
©2006 American Machine & Tool Co., Inc. of PA, A Subsidiary of The Gorman-Rupp Company, All Rights Reserved.
Periodic maintenance and inspection is required on all pumps to insure proper operation. Unit must be clear of debris and sediment. Inspect for leaks
and loose bolts. Failure to do so voids warranty.
1 Inch Self-Priming Centrifugal Pumps
Refer to pump manual 1808-634-00 for General Operating and Safety Instructions.
Description
These centrifugal pumps are self-priming (to 6 ft. lift) units designed for transferring perchlorethylene (and other non-flammable liquids) from drums or
storage tanks. Handle liquids from 40º F to 180º F (4º C to 82º C). Units should be used only with non-abrasive, non-flammable liquids that are
compatible with pump component materials.
Maintenance
Make certain that
power source is
disconnected before
attempting to service or disassemble any
components! If power disconnect is out-of-
sight, lock it in open position and tag it to
prevent application of power.
MECHANICAL SEAL REPLACEMENT
Refer to Figures 2 and 3.
IMPORTANT: Always replace both seal seat
and seal head to insure proper mating of
mechanical seal components!
NOTE: It is not necessary to remove piping
from pump casing. The motor and impeller
assembly are removed from back of casing.
1. Drain pump before disassembling.
Unscrew pipe plug (Ref. No. 13) to drain
most of liquid; some will be left in bottom.
2. Unthread hex nuts (Ref. No. 4) and
remove pump casing (Ref. No. 12) and o-
ring (Ref. No. 7) from casing cover (Ref.
No. 6).
3. To unscrew impeller (Ref. No. 11), turn
counterclockwise (CCW) facing impeller.
Unscrew acorn nut (Ref. No. 16) and o-
ring gasket (Ref. No. 15) before
unscrewing impeller.
NOTE: A screwdriver slot or two flats for use
with an open end 7/16" wrench are provided at
rear of motor shaft (remove bearing cap for
access). To hold motor shaft from turning,
either insert a large screwdriver blade into the
slot, or use a 7/16" wrench across the flats.
4. Unthread cap screws (Ref. No. 5) and
remove motor adapter (Ref. No. 3). Seal
head (Ref. No. 9) and impeller shims (Ref.
No. 10) will come loose at this time.
NOTE: Casing cover will still be attached to
motor adapter.
IMPORTANT: Retain impeller shims for use
when reassembling unit.
5. Push seal seat (Ref. No. 8) from casing
cover with screwdriver.
6. Clean adapter recess before inserting a
new seal seat.
7. Carefully wipe polished surface of new
seal seat with a clean cloth.
8. Wet outside of rubber portion of seal seat
with a light coating of soapy water.
9. Press new seal seat squarely into cavity in
casing cover. If seal seat does not press
squarely into cavity, it can be adjusted
into place by pushing on it carefully with a
piece of pipe or dowel. Always use a
piece of cardboard between pipe and seal
seat to avoid scratching seal seat. (This is
a lapped surface and must be handled
very carefully).
10. After seal seat is in place, insure that it is
clean and has not been marred.
11. Using a clean cloth, wipe shaft and make
certain that it is perfectly clean.
12. Carefully guide motor shaft through seal
seat. Secure motor adapter on motor
mounting face.
13. Apply a light coating of soapy water to
inside rubber portion of seal head and
slide onto shaft (with sealing face first) so
that rubber portion is just up over shaft
shoulder.
Do not touch or wipe
face of polished part of
the seal head.
14. Replace any impeller shims which may
have been removed in dis- assembly
(see "Shim Adjustment").
15. Screw impeller back in place,
tightening until it is against shaft
shoulder. Replace o-ring gasket and
acorn nut.
16. Remount o-ring and pump casing on
casing cover.
IMPORTANT: Always inspect o-ring gasket
for cracks or cuts when unit is
disassembled. Replace if damaged.
SHIM ADJUSTMENT
When installing a replacement impeller
(Ref. No. 11) or motor (Ref. No. 1), it may
be necessary to adjust number of shims
(Ref. No. 10) to insure proper running
clearance between impeller and casing.
Proceed as follows:
NOTE: A proper running clearance is less
than 0.010.
1. For impeller replacement, add one
0.010" shim in addition to shims
removed originally.
2. For motor replacement, add two
0.010" shims in addition to shims
removed during disassembly.
3. Reassemble pump using "Mechanical
Seal Replacement" for reference.
IMPORTANT: Insure that casing is in place
and check shaft to make sure it is turning
freely (use screwdriver slot or two flats at
rear of motor to turn shaft). If it turns freely,
check to insure that casing cover and
casing are fitted metal-to-metal where they
meet on outside. If they are not metal-to-
metal, tighten the hex nuts (Ref. No. 4) and
recheck shaft for free turning. Tighten,
carefully turning shaft while tightening so
that motor bearings are not damaged in
event that too many shims were installed. If
shaft seizes before fasteners are
completely tight, disassemble pump and
remove one shim and repeat reassembly.
Specifications Information and Repair Parts Manual 4294-98 thru 429N-98
4294-251-00 08/2007